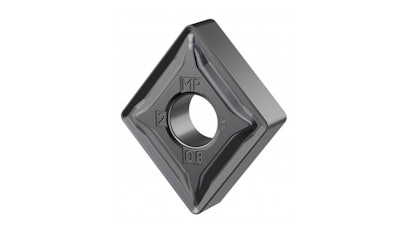
Kennametal has introduced its newest and most advanced turning grade, KCS10B, for nickel, cobalt and iron-based superalloys used in aerospace and other high temperature applications.
KCS10B, which features a revolutionary coating applied to an ultra-fine grain carbide substrate for superior layer adhesion, delivers up to 50% greater tool life, more predictable processes, and improved productivity when working with difficult to machine superalloys.
KCS10B overcomes the most common challenges encountered in turning superalloys — cratering and depth-of-cut notching — two wear modes that often lead to unexpected and even catastrophic tool failure.
The secret behind KCS10B is Kennametal’s proprietary High-Power Impulse Magnetron Sputtering (High-PIMS) technology. Rather than the light rain of droplets that fall on cutting tools during traditional PVD coating processes, High-PIMS generates a fine mist of AlTiN, building a series of “extremely thin, smooth, and wear-resistant layers.”
Metals such as Inconel 718 and Stellite 31 are notorious for causing rapid wear and unpredictable tool life. KCS10B is proven to reduce DOC notching and extend tool life from 3 minutes to upwards of 5 minutes in roughing operations. Tool life in finishing operations fares even better, with visible cratering and subsequent tool failure often delayed by a factor of two or three compared to competitive brands.
Depth-of-cut notching and crater wear are far more manageable thanks to the super smooth coating and special edge-prep of inserts coated with KCS10B.
Learn more at www.kennametal.com.