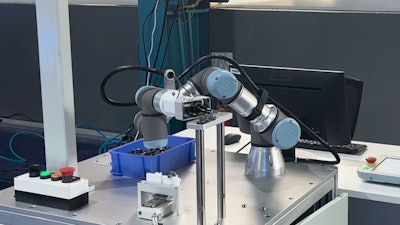
In our fast-paced, automated world, it’s becoming increasingly important for manufacturers of all sizes to implement robotic systems wherever possible to keep up with the competition. Pick and place robots, in particular, offer significant advantages, enabling companies to improve their throughput, reliability and safety in various industries, particularly when it comes to traditionally monotonous or time-consuming tasks like sorting, inspection and assembly.
However, the high upfront costs, complex implementation processes and limited accessibility of pick-and-place robotic technologies have traditionally posed obstacles for many businesses. The hardware alone in these systems can easily cost tens of thousands of dollars or more, not to mention the high costs and labor demands associated with implementation.
Fortunately, there are now low-cost robotic options for manufacturers looking to automate their pick and place operations. Systems are available through an online platform that breaks down the automation solutions into individual components and then finds the lowest-cost parts that still meet the system’s required specifications. By aggregating key components in this way, the platform empowers users to design, build and purchase a pick and place system that meets their unique application needs.
Here is how this robotic platform provides an easy, user-friendly and cost-effective automation onramp for pick and place operations, enabling manufacturers to unlock greater productivity, reliability and cost savings.
Exploring the igus® RBTX Platform
The igus® RBTX platform lowers the barriers to automation by making a broad range of robotic technologies more accessible to companies. It accomplishes this task by addressing two large sources of cost that often prohibit manufacturers from adopting automated solutions. The bulk of the cost is typically due to the hardware, along with getting the hardware up and running. By providing affordable equipment and simplifying the integration process, RBTX has made these two sources the pillars upon which the entire platform is built. Here’s how:
- Hardware. The many elements involved in an automated solution can make finding affordable solutions a hassle. RBTX breaks down and aggregates individual, low-cost components from leading manufacturers.
- Implementation. Complex implementation often discourages manufacturers from adopting automated pick and place technologies. RBTX simplifies this process by consolidating all necessary information into a single place, saving users time otherwise spent on research. It also offers consultation and testing services, guaranteeing the feasibility of the robotic system before it is delivered. For example, the platform’s “RBTXpert service” includes remote integration support, video consultations and live application tests, ensuring solutions are effective prior to delivery.
A Scalable Automation Roadmap
Through its cost-effective product offering, user-friendly platform and supportive services, RBTX promotes the accessibility of automated pick-and-place solutions, empowering manufacturers to improve their operational efficiencies and gain a competitive edge in the market.
For pick-and-place tasks, in particular, RBTX solutions can take many forms and vary in cost and complexity. Once a system has been tested and implemented, it’s easy for users to expand their operations and install more of the same system without repeating the integration process. This strategy allows businesses to start small and expand production while reducing upfront costs.
For example, ideal for many small and medium-sized businesses is the delta robot that starts as low as $4,935.36 — which is nearly 50 percent less than competitor price points. Not only is this hardware less expensive up front, but it also incorporates self-lubricating materials that reduce routine maintenance requirements, minimizing long-term costs. Each one is designed with drylin® linear actuators that feature highly engineered, self-lubricating sliding plastic liners, eliminating the need for external lubricants and making liner replacement a quick and easy process. These delta robots provide rapid return on investment (ROI) and are ideal for many low-cost applications like belt transfer stations and sorting systems, small parts handling and fast positioning machines.
Another RBTX option for pick-and-place operations is the six-axis ReBeL® robotic arm, which offers six degrees of freedom for greater application flexibility. Starting at just under $4,500.00, this solution is compatible with various end effectors, camera systems and accessories and is even suitable as a collaborative robot, or cobot. It is up to two times lighter than other cobots and integrates the control system in its base, eliminating the need for a cabinet.
Moving up the ladder in terms of cost and complexity, users can even find everything they need to design an entire robotic work cell. For example, a ReBeL® arm, vacuum gripping system and cell would cost just over $14,448.00. To customize their pick-and-place workstation, users can tap into the Machine Planner function, which handles all the engineering work required to design and combine the robotic components.
RBTX Robotic Systems for Pick and Place Applications
The versatility and flexibility of pick-and-place robots allow them to be used for many industrial applications like sorting, bin picking, packaging, inspection and assembly. Here’s a rundown of what’s possible when designing a pick and place system using RBTX:
Single or multiple cobots. In one use case, the six-axis ReBeL® cobot performs pick and place tasks with the help of a vacuum pump. This robot is ideal for collaborative applications due to its compact design, 360-degree rotatable joints and ability to lift payloads up to 2 kilograms. Two ReBeL® cobots can even be configured to work synchronously with each other, creating a solution that is more cost-effective than a single industrial robot.
Picking and placing with the ReBeL® robot.igus
Vibration table picking. Manually presorting screws, nuts, O-rings, and other small components drives a lot of time and is a very monotonous process. A vibration table, combined with a delta robot installed above it, offers an economical solution to precisely presort these components, making them available to employees for the next step in the production process. Able to be installed next to the assembly line, this compact system consists of an igus® delta robot, separation machine and camera system.
Automated chocolate dispensing. Dubbed the “ChocoMatic,” this robotic pick and place system consists of a robolink® robotic arm mounted on an igus® guide. End users can use a smartphone or tablet to control the robot as it picks individual chocolates from a pallet and then places them in a box. This system is equipped with a camera to take pictures of all the chocolates. Using this data, it automatically learns where the various chocolates are located. It can also measure the height of individual treats and will use this information later when filling the box.
Taking the cost-effectiveness of the system even further, the robolink® arm does not require costly, recurring licenses. Its small size also makes it ideal for smaller applications, making it a compelling, profitable attraction for food stores or museums. It also offers a more hygienic solution since the chocolates don’t come into contact with people.
Conveyor belt picking. In one application, an igus® SCARA robot, equipped with a high-precision gripper, picks up individual items from a moving conveyor belt and places them in a predefined location. This robot offers fast, accurate movements, which are ideal for handling small- and medium-sized objects.
An example of a robotic system for conveyor belt picking.igus
Machine tending of gear shafts. This application from a 3D vision manufacturer highlights the option to implement intelligent camera systems to enhance handling processes. The system includes a six-axis cobot, which picks up unsorted gear shafts with the help of a camera system. It then places the parts in a fixture for inspection.
The Advantages of Low-Cost RBTX Solutions
Adopting RBTX robotic systems for pick-and-place applications offers several benefits, enabling manufacturers to automate processes they have never automated before. In doing so, they can improve the following:
- Productivity. Since robotic systems can work around the clock, they’re inherently more productive than humans, translating to higher throughput.
- Reliability. Robots aren’t prone to mistakes the way humans are. In fact, pick-and-place robots offer accuracy within one millimeter over the course of their entire service life.
- Safety. Compared to humans, robots are a safer choice for picking and placing. This not only improves safety but also allows workers to focus on more complex tasks, thereby increasing overall productivity.
- Return on investment. Since pick-and-place robots can work faster and more efficiently than humans, they provide a faster ROI. Although the initial investment is higher with robots, they’re a more cost-effective option in the long term. This is especially true of the offerings available through the RBTX platform, many of which incorporate maintenance-free, self-lubricating materials.
- Flexibility. Due to their modular nature, manufacturers can easily adapt and reconfigure RBTX systems for different pick-and-place tasks. This flexibility is a big advantage for manufacturers that must respond quickly to changes in production requirements.
- Ease of programming. Users can easily program the RBTX robots using free robot control software that doesn’t require prior programming knowledge, driving even greater adoption in the manufacturing community.
Common Pick-and-Place Robots
- Gantry robots. These linear robots move along three planes (X, Y and Z), offer high positional accuracy and can cover larger workspaces than other pick-and-place robots.
- Delta robots. These parallel robots consist of three arms connected to a common joint above and below the arms. Their biggest advantage is speed, which often comes at the cost of lower payloads compared to other robots.
- Robotic arms. These five- and six-axis arms are the most commonly used pick-and-place robots due to their versatility. Their freedom of movement makes them well-suited for applications requiring complex movements.
Get Started
The use of RBTX robotic systems in robotic pick-and-place applications demonstrates the ability of low-cost automation platforms to transform industrial processes.
RBTX is an online portal for low-cost robotics that connects users and suppliers of cost-effective robotic components.igus
Available in simple to complex configurations, they offer a compelling solution for manufacturers of all sizes, empowering them to take automation further than they’ve gone before.
For more information, visit rbtx.com.