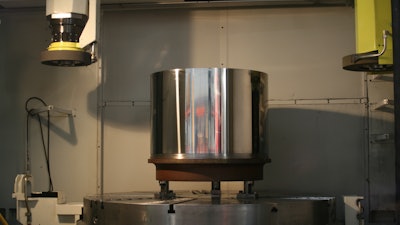
In 2008, a French machine manufacturer commissioned the development of a grinding machine for high-precision internal and external machining of tubular rollers.
Equipped with hydrostatic components from Hyprostatik, including guides, rotary table and grinding spindles, the machine achieved a surface finish of Ra 0.003 micrometers during acceptance testing. Now, 17 years later, it achieves a value of Ra 0.016 micrometers with the hydrostatic components unchanged.
The advantages of hydrostatic technology lie in the virtually friction-free and highly rigid bearing provided by hydrostatic pockets, which enable precise positioning in the sub-micrometer range. Compared to rolling systems, hydrostatic systems offer improved damping and lower heat generation, which increases precision and surface quality.
Even at higher speeds, rotary tables with hydrostatic bearings prove to be extremely thermally stable.Hyprostatik
Thanks to active control of the oil flow by PM controllers, the gap stiffness is three to six times higher than with conventional hydrostatic systems. The grinding machine operates with two hydrostatic grinding spindles for simultaneous internal and external grinding and enables automatic change of grinding wheels thanks to an HSK100 clamping system.
The hydrostatic bearing of the rotary table with a 2,000-millimeter diameter plate is designed for workpieces that weigh up to 10,000 kilograms at a maximum speed of 80 revolutions per minute.
The hydrostatic axial bearing with PM-flow controller and the complete hydrostatic radial bearing supplied result in flatness and concentricity values of less than 1 micrometer, which is copied onto the flatness and roundness of the workpiece.