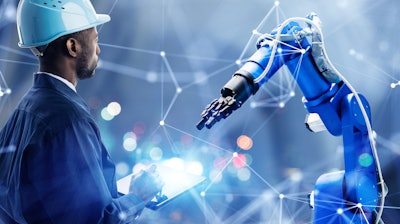
In many ways, a robot’s efficacy relies on its sensors. Autonomous systems must be able to make sense of the world around them to interact with it appropriately, but that can be difficult in dynamic environments. Multimodal sensor fusion for robots provides a way past this obstacle.
Multimodal sensor fusion combines input from different kinds of sensors. With a broader range of data, robots can make more informed decisions, which has several practical benefits for end users.
1. Increased Accuracy
The primary advantage of sensor fusion for robots is higher accuracy. Even though many manufacturers use robotics to reduce human error and improve efficiency, 81% encounter robot-led production shutdowns, suggesting automation isn’t always as reliable as it initially seems.
Multimodal sensor fusion can prevent these errors by improving robot decision-making. Misjudgments are fairly easy to make if a machine can only base its decisions on a single factor, even within a predictable workflow. By the same token, robot accuracy improves as this equipment gathers more data to inform its decisions.
Because multimodal sensor fusion provides a more diverse data set, it minimizes a robot’s room for error. As a result, robots can identify objects, measure physical space or make other decisions more confidently, preventing mistakes and maximizing resource and time efficiency.
2. Added Flexibility
This data diversity also makes robots more versatile. Some robotic systems may not need accuracy improvements — with some pneumatic arms featuring up to two-millimeter precision and 0.02 mm repeatability — but only achieve that level when workflows are predictable. Sensor fusion makes automation more forgiving.
With multiple inputs, if one sensor fails to portray a situation accurately, another can fill in the gaps. Removing single points of failure ensures your robotic systems can maintain peak performance across a wider, more consistent range of scenarios.
Similarly, because sensor fusion increases the range of data a robot can measure, it can enable a single robot to perform more tasks. That versatility is an important selling point in a market where upfront costs are often high.
3. Higher Efficiency
Another advantage of sensor fusion for robots is it can increase efficiency. Much of this productivity boost comes from sensor fusion’s higher reliability.
Because robots using multiple sensors to make decisions produce fewer errors, they result in less unexpected downtime. Considering facilities experience an average of 20 unplanned downtime incidents monthly, each lasting more than an hour, that error reduction can produce significant improvements.
Sensor fusion can also increase efficiency by reducing computational complexity for multi-sensor systems. A single algorithm will analyze data from each sensor simultaneously instead of compiling results from separate systems. As a result, multi-sensor robots can make accurate decisions faster.
4. Improved Safety
Multimodal sensor fusion makes robots safer to work around. Many facilities embrace automation to reduce workplace accidents, but robots themselves can endanger workers if they get too close. Sensor fusion minimizes this risk by improving robots’ ability to sense and avoid humans.
Human employees can be difficult for conventional robots to detect because people move and behave unpredictably. However, if a robot can sense its surroundings through multiple systems — such as machine vision, motion sensing and location sensors — at least one of those sensors will likely detect a person.
Increased detection reliability minimizes the chances of a robot colliding with a worker. Employees can then work safely around collaborative bots without fear of injury, and facilities can reduce accidents and related expenses.
5. Reduced Complexity
Using sensor fusion for robots also reduces the complexity of the robotic data-analysis process. That’s because multimodal sensor fusion is about more than just equipping a robot with multiple sensors. It also uses algorithms to streamline data processing and analysis.
Sensor fusion lets you preprocess data from multiple inputs and analyze it in a single pass. Because it’s a software-defined process rather than a matter of hardware, it’s also easier and cheaper to build into robots than having to incorporate several separate sensor systems.
This reduced complexity makes robotics implementation as a whole more cost effective. Considering 71% of automation adopters cite high capital costs as their leading obstacle to robots, that user-friendliness is significant.
Applications of Sensor Fusion for Robots
Making the most of these benefits of sensor fusion for robots requires understanding where these systems are most impactful. Virtually any robot can benefit from this technology, but some use cases stand to gain more than others.
Autonomous Vehicles
Autonomous guided vehicles (AGVs) are one of the best applications for multimodal sensor fusion. Sensor fusion helps AGVs navigate more effectively, ensuring they get where they need to on time and avoid collisions.
Ideal sensors to integrate into AGV sensor fusion systems include vision, LIDAR, motion capture and radio frequency beacons. Combining two or more of these on an AGV will ensure safe, efficient navigation even if one system fails. That’s crucial in workplaces where AGVs and human workers share a common space or where inventory locations shift.
Cobots
Cobots are another ideal use case of sensor fusion for robots. They’re the fastest-growing industrial robot subsector but can be difficult to implement, as the humans they work with aren’t always predictable. Working so closely with employees introduces safety concerns, further making the case for sensor fusion.
Sensor fusion for cobots should focus on systems that help these bots detect and avoid contact with employees. Navigation technologies may also be necessary if the robots are mobile, as many cobots are.
Quality Control Automation
Multimodal sensor fusion is ideal for quality control workflows. Many facilities use machine vision systems to improve efficiency and reduce errors in quality inspections, and sensor fusion can take these benefits further.
Combining data from multiple sensor types lets robots inspect a product along more criteria, minimizing the chances of missed defects and letting a single system perform numerous checks. That consolidation can mitigate bottlenecks that often arise in quality control.
Robotic Sensor Fusion Unlocks Automation’s Potential
Multimodal sensor fusion for robots makes automation more reliable, efficient, versatile, safe and accessible. Those improvements address many of robotics’ most common obstacles, making automation a more justifiable investment for many businesses. As this technology grows, it could help manufacturing and similar industries experience automation to its fullest potential.