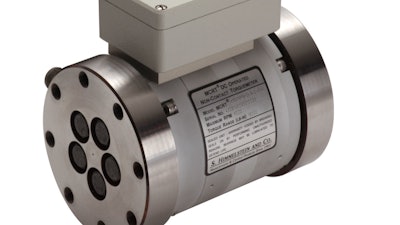
Businesses purchasing torque sensors are sometimes unaware of the significant impact a torque sensor’s performance can have on their bottom line. Small inaccuracies in torque measurement can have a significant impact on the durability and efficiency of a company’s products. Reliable torque data leads to more efficient and cost-effective designs. Unfortunately, torque sensor manufacturers are not always consistent in how they represent the performance of their product lines.
In particular, torque sensor nonlinearity specifications are determined in many different ways, as there is no accepted standard. Manufacturers will sometimes take advantage of this and use tricks to make their torque sensors seem better than they really are. Others use methods that are appropriate for static torque loads, but are not accurate for the dynamic torque loads found in the real world.
It is therefore critical to not just know a sensor’s specifications, but to understand how they are determined by the manufacturer — in particular, how the manufacturer quantifies the nonlinearity of their torque sensors.
Problems with calculating torque sensor nonlinearity
Historically, nonlinearity and hysteresis definitions were developed to characterize performance of common sensors such as scales and load cells. Those definitions are widely used to characterize torque sensors. Despite the similarities between torque sensors and weighing devices, there are significant differences between them and their applications. Most important, real-world torque signals are dynamic whereas weighing and most load measurements are primarily static.
Applying those traditional definitions to torque sensors can result in misleading and incorrect conclusions. These methods take the output signal points for increasing loads and creates a reference line. The furthest deviation from this reference line is considered the nonlinearity value. Although this is an effective method for calculating nonlinearity for static loads, rotating torque output signals are dynamic and thus more complicated. Linearizing a dynamic torque signal consisting of sinusoidal components, torque reversals and inertia will only generate additional errors. Unfortunately, most manufacturers ignore this difficulty and apply the method described above.
To further complicate the issue, this approach is often inconsistently implemented, since the reference lines can be determined in a number of ways. Most U.S. manufacturers traditionally use a line connecting the first and last load points of the increasing torque load output signal as the reference line for the output signal. However, European manufacturers use a best fit line through the first load point.
Other approaches to determine the reference line for calculating the nonlinearity include using a best fit through zero using increasing torque load data only; using a best fit line through the first load point including only increasing torque load data; using a best fit line through the first load point using many data points for increasing torque loads; and only a few data points when torque loads are decreased (asymmetrical loading). None of these methods are invalid because there is no set standard. They are all simply trying to draw a line that can be used to determine the largest deviation that the true output signal makes from that reference line.
With all these different methods for determining the reference line, it becomes impossible to reliably compare torque sensors from different manufacturers using the resulting calculated nonlinear values. In the absence of a standard approach for calculating the nonlinearity of the output signal of a torque sensor, it is necessary to understand the pitfalls of the respective methods. For instance, an approach that uses a low number of data points to determine the nonlinearity can underestimate the nonlinearity of the output signal. Ignoring or deemphasizing decreasing torque load output signal data misrepresents the significance of hysteresis.
Some manufacturers will linearize the calibration stand response of a nonlinear torque meter. Although linearization can yield a very linear response on the calibration stand, it will produce significant additional errors in real-world dynamic applications. The reported average torque will be in error and frequencies not present in the input signal will be generated. A torque meter that includes linearization software may improve the linearity of the static calibration, but in dynamic, real-world applications it will generate additional errors.
A better approach for calculating nonlinearity
To determine a torque sensor’s nonlinearity, ascending and descending loads (usually 10 CW and 10 CCW) are applied from a low uncertainty, accredited torque calibration stand and the outputs recorded. Nonlinearity is defined as the output’s greatest deviation of ascending data from a reference line that emulates the torque sensors ascending response. This value is expressed as a percentage of full scale. During the calibration, the difference between the ascending and descending outputs at each load point is also calculated. Hysteresis is defined as the greatest difference between those values. It also is expressed as a percentage of full scale.
The conventional definition of nonlinearity does not include the descending response. Since virtually all torque measurements are dynamic and include torque oscillations and reversals, the descending portion of the response curve must be included to accurately depict the torque sensor performance including hysteresis effects.
The more practical approach to representing a torque sensor’s performance is to calculate a combined error taking into account both nonlinearity and hysteresis. Using all ascending and descending calibration data, compute a best fit reference line (BFL) for both CW and CCW directions. Then the greatest deviation for the BFL is found for CW and CCW loadings. The torque sensor’s combined nonlinearity and hysteresis is the greater of the CW and CCW deviations. This approach has the advantage of accounting for ascending and descending response while intrinsically accounting for hysteresis. The resultant combined error value may be larger than what most manufacturers quote using other methods, but is a more accurate representation of the torque sensor performance in the real world.
Why nonlinearity is important
To avoid errors, a torque sensor’s output must faithfully reflect its input. When an output signal is nonlinear, calculations such as average torque contain errors. Nonlinearity also creates output frequencies not present in the input torque, including harmonics of the input frequencies. To minimize these issues, it is essential to use a torque sensor with minimal, correctly characterized nonlinearity.
Accurate torque sensor measurements are critical to the development and testing of products such as motors, compressors, pumps or any power-generating or power-consuming equipment. Inaccurate torque readings can lead to inefficiencies and shorter product life cycles. These in turn can lead to unexpected expenses and downtime. Inaccuracies during the R&D cycle can lead to delays and increased product development costs. Engineering teams working with torque sensors with accurately characterized nonlinearity are able to exactly dial in products, with no guesswork, providing a competitive advantage in time-to-market.
Today, there is no set standard for determining torque sensor nonlinearity. Popular approaches employed were borrowed from procedures for determining nonlinearity in sensors with static loads, such as load cells. This approach is a rough estimate at best as torque sensors mostly deal with dynamic loads in the real world. The various methods for determining reference lines for calculating nonlinearity are inconsistent and misleading at best. These methods, which employ linear fits or load points as fixed end points, often fail to capture the full picture of a torque sensor’s signal response. Namely, that there exists a hysteresis between the signal output of increasing torque loads as compared to the signal output of decreasing torque loads.
An accurate quantification of nonlinearity requires consideration of hysteresis when calculating the best fit reference line. This reference line can be used to calculate nonlinearity more accurate to real-world applications where rotation and inertia are involved. Unfortunately, these nonlinearity values can appear large compared to less rigorous approaches. Thus, it is imperative when specifying torque sensors to understand the method used for calculating nonlinearity. It will require some extra research, but the resulting understanding will save money over the long term.
Steve Tveter is vice president at S. Himmelstein and Company.