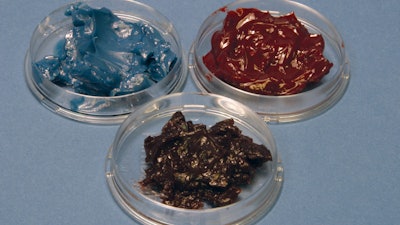
Grease is a lubricant that is used in roughly 80% of all bearings globally. In hardworking machines, grease reduces friction and wear, prevents corrosion and keeps maintenance costs from mounting. From steel mills to cement plants to all types of industrial facilities and every size of mobile equipment, the right grease can extend bearing life in critical equipment, while testing can identify the specific grease properties that are most important to your bearings, making it possible to select a formulation that outperforms all others.
Machines are becoming bigger, faster and more powerful across every industrial sector, demanding stronger bearings to keep operations moving reliably. And while new bearing designs can offer new advantages, often it can be just as effective to improve lubrication practices to eliminate unexpected repairs and prevent downtime. Operators constantly challenged to increase plant efficiency and cut maintenance spending should keep these considerations in mind when it comes to bearing grease:
No Two Greases Are Perfectly Alike
Every grease is a unique formulation having different functional properties, with the ingredients and quantities used in the manufacturing process having significant influence on the final product. While it is difficult to know all the ingredients that might go into a grease, it can be helpful to understand how certain additives and agents impact performance. Take a closer look and you will find that:
- Base oils account for 60% to 90% of grease composition. Petroleum-based mineral oil, the most commonly used base oil (about 90% global share), is inexpensive and suitable for a wide range of applications. Synthetic oils, meanwhile, can yield wider operating temperatures and longer life. These tend to include polyalphaolefins (PAOs), esters, perfluoropolyethers (PFPEs) polyglycol (PAG) and silicon-based oils.
- Thickening agents constitute 3% to 40% of grease formulation and can be of different types: soaps, complexes, mixed soaps and nonsoaps. Soap greases (including soda, sodium, calcium, lithium and aluminum) are an economical choice for applications with operating temperatures up to 121°C. For greater temperature demands, complex greases such as calcium complex, aluminum complex or lithium complex are preferable. Lithium calcium, meanwhile, is one example of a mixed soap ideal for high-temperature applications where good water resistance is also required. Furthermore, there are nonsoap greases (thickened with polyurea, clay and Teflon™) suited for very high operating temperatures due to their excellent resistance to temperature change.
- Additives make up the remaining 1% to 10% of most greases. There are many types of additives, including rust inhibitors that provide a barrier to water or oxidation inhibitors that slow the rate at which greases break down. There are also antiwear additives that help prevent metal-to-metal contact between the bearing surfaces or extreme-pressure additives that reduce the likelihood of scuffing wear or shock loading (these include sulfur- and phosphorous-based additives as well as solid lubricants like molybdenum disulfide and graphite). In addition, polymers are frequently used to modify the viscosity of grease or to make greases tackier.
Consulting with a bearing or lubrication expert is the best way to learn about the grease characteristics that are most vital to your application―even one phone call or plant visit can result in recommendations for a smoother-running operation.
Other Factors Affecting Grease Performance
Grease composition is only half the equation. Bearing life also depends on proper lubrication practices. Improper lubrication is by far the leading cause of bearing damage (more than 50% of all bearing damage) and can be generally classified into the following categories:
- Overfilling a bearing with grease can cause churning, resulting in excessive heat and purging (where grease leaks from the bearing). As the operating temperature rises, the oxidation (breakdown) rate of the grease increases, doubling every 18°F (10°C). Note that during initial startup, it is common for a properly lubricated bearing to purge a small amount of grease.
- Underfilling a bearing can generate heat but for different reasons. This condition is known as grease starvation and can cause excessive metal wear. If a bearing suddenly becomes noisy and/or the temperature increases, it may be due to insufficient lubrication.
- Water contamination causes grease to have a milky white appearance. The presence of as little as 1% water in grease can make a significant negative impact on bearing life.
- Worn-out grease has seen time and temperature conditions deplete its oil-release properties, where the thickener and additives have decomposed and broken down. There is no option other than to replace the grease immediately.
- Mixing greases may cause the new mixture to soften and leak out of the bearing (due to incompatibility of the thickener) or to become lumpy, discolored and hard. Always lubricate bearings with the same type and consistency of grease. If this is not possible, consult an expert to determine a compatible substitute.
- Inconsistent lubrication intervals can lead to excessive oxidation and premature bearing wear. It is critical to follow manufacturers’ relubrication schedules exactly, with technicians recording key data on a bearing maintenance sheet.
- Incorrect type, which could include using the wrong base oil viscosity, thickener type or additive package, can also lead to premature bearing damage.
Testing Can Determine the Optimal Grease
A technical evaluation can be conducted when the impact of grease properties on bearing performance must be closely understood. To help customers meet this challenge, Timken operates world-class lubricant-testing facilities equipped with the talent, tools and technologies for analyzing different greases.
Testing can provide valuable insight into grease integrity and durability. While there are many methodologies that can be applied, common approaches to grease analysis include:
- Oxidation Stability Evaluation (ASTM D942): Oil oxidation, which is time- and temperature-dependent, directly affects grease life by diminishing its ability to form an effective lubricant film on bearing contact surfaces. Consequently, greases having significant oxidation stability are better suited for applications with high operating temperatures and long service period requirements.
- Rust and Corrosion Evaluation (ASTM D6138): Moisture ingress is common in many machines and can lead to corrosion or water etching on bearing surfaces. Severe corrosion can cause surface pitting or subsurface fatigue damage. Testing can dial in the degree of rust and corrosion protection provided by the bearing grease.
- Extreme Pressure Performance and Wear Evaluation (ASTM D2596 and ASTM D2266): Greases have different load-carrying capabilities and wear-preventive characteristics. Analysis can reveal which formulations offer low, medium or high levels of extreme-pressure performance and which provide superior wear resistance over time.
Kuldeep Mistry, Ph.D., is a research and development specialist at The Timken Company.