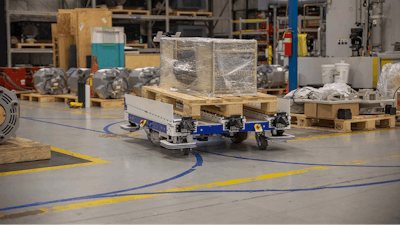
Automated guided vehicles (AGVs) are driverless vehicles that use computer software and other navigation technologies to determine their positioning and movement. They can transport various materials and finished goods within a manufacturing facility or warehouses. Basically, if you are interested in digitalizing your material handling system, then this technology is something you are looking for.
There has been an increasing adoption rate of AGVs across various industries. According to Fortune Business Insights, AGVs global market size was $1.83 billion Uin 2020. The market is predicted to grow at a CAGR of 9.3 percent and reach 3.72 billion U.S. dollars by 2028.
Types of AGVs
Automated Guided Carts are mobile platform robots characterized by low-profile, small chassis and engage shelves, trolleys, or carts from underneath. An AGC, also referred to as an Under Ride, has minimal features and is the most basic type of AGV.
Their navigation systems can range from simple magnetic tapes to complex sensor-based systems that rely on artificial intelligence to navigate. AGCs are easy to install, low cost, flexible, and enhance safety making them ideal for automating non-value-added tasks. They eliminate the need for humans to push carts and trolleys around.
There are two types of AGCs, distinguished by how they engage the load. These are AGCs with pin hooks and AGCs with lifting devices. AGCs with pin hooks rely on pin hooks to engage trolleys of carts with wheels. It engages the cart and pulls it while the cart’s wheels support the load weight. In addition, they are lighter and allow decent towing rates with limited power since the cart supports the weight.
On the other hand, AGCs with lifting devices lift the entire load and perform more advanced navigation tasks. AGCs can effectively transport compact loads and have wide applications in hospitals, e-commerce, and warehousing.
Towing AGVs are also known as AGV tugger vehicles and are designed for towing carts. They have greater throughput than AGCs because they can haul multiple carts simultaneously. They are an excellent option for intra-logistics optimization because they offer exceptional transport capacity at a low cost. Tugger vehicles pull loads of tons reducing the risks of using large and heavy equipment. These AGVs can move loads of up to 50,000 pounds. Heavy-duty towing AGVs can pull sub-assemblies, equipment, machine components, and materials that would be unsafe for manual labor.
The main applications of towing AGVs are the automotive and manufacturing industries. They feed production lines with materials and assist with finished goods removal in manufacturing industries. The automotive industry uses tugger vehicles to supply parts to the assembly lines. For example, automated guided vehicle systems are in use at Audi, and they are used for delivering materials and components for production just in time and exactly where they are needed.
Even though towing AGVs have numerous benefits, there are several drawbacks to be concerned about. Tugger vehicles cannot hook carts autonomously and have complex hooking and unhooking techniques. There are also safety concerns around towing AGVs because they consist of several carts independent of the locomotive.
Automated forklifts are mechanized forklifts that can place materials, retrieve stock, and stack or place pallets. They supply materials to computerized machines and take finished goods to the storage or for shipment. Heavy-duty automated forklifts can transport heavy loads such as steel coils, vehicles, large paper rolls, and engines over any distance. The key benefit of automated forklifts is replacing forklift operators who need training and certification. They can also be economical by reducing labor costs. Automated forklifts are primarily used in warehouses and manufacturing facilities.
There are several types of automated forklifts which include:
- Automated Pallet Jack: The automated pallet jack is, also referred to as Pallet Mover AGVs, are designed to transport palletized loads in warehousing and manufacturing facilities.
- Automated Forklift Truck: This forklift is used when it is impossible to have support legs below the forks. They are versatile and are designed to handle heavy payloads.
- Very Narrow Aisle AGV (VNA): VNAs are designed to perform high lifting loading operations in very narrow aisles.
- Reach Truck AGV: Reach trucks are also designed to handle tasks in narrow aisles but are smaller, faster, and can take more weight than VNAs.
Unit load AGVs handle discrete loads like individual items or a single unit like a tote or pallet containing multiple items. They usually are equipped with roll conveyors. In addition, unit load handlers can navigate safely and fast in production facilities and warehouses. They handle loads from automated storage and retrieval systems (AS/RS), stands, conveyors, and end-of-line equipment. They are suitable for delivering packages, which may be heavy and hazardous for manual labor, to predetermined locations within a facility.
Unit load AGVs have wide applications in the Food and Beverage industry. They offer an efficient and flexible solution for transferring materials to and from fixed conveyors. Unit load AGVs with in-built conveyors are ideal for increasing the functionality of conventional conveyor systems.
Facility managers can equip unit load handlers with automatic transfer systems to transport and shift the load. These systems include: roller conveyors, lift platforms, chain conveyors, shuttle systems and belt conveyors.
How to Choose the Right AGV
There are many types of AGVs with different applications in various industries. All these types are critical in quality materials handling and none is better than the other. Every facility has its own ideal AGV type that will depend on user requirements and expectations. Some facilities need custom material handling carts and there are companies that can provide this kind of equipment.
The first step to choosing the right AGV is conducting a needs and requirements assessment on your facility. Once you have identified the tasks you want your AGV to handle, you can choose an AGV that effectively handles them. The right AGV for you will also depend on your budget and the technical skills required to manage and maintain the system.
Luke Goodwin is an experienced marketing manager with a demonstrated history of working in the logistics and supply chain industry. Currently, he works as a CMO at FlexQube. To learn more about FlexQube and see more articles from the industry you can visit their news website.