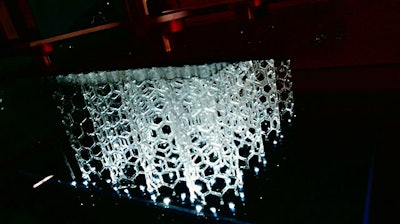
Researchers from Northwestern University say a newly developed 3D printer offers the speed and quality to enable additive manufacturing to compete with conventional manufacturing techniques.
The HARP — or high-area rapid printing — offers unprecedented throughput without sacrificing the resolution of the print, Northwestern scientists said. The 13-foot printer can produce about 1.5 feet of printed material per hour on a 2.5-square-foot print bed, and can make either a single, large part or simultaneously print many different, smaller parts.
The researchers expect the system to be available commercially within 18 months. Their study was published in the journal Science.
The HARP, engineers noted, uses a technique known as stereolithography, which prints liquid resin into hardened plastics. Ordinarily, those systems become extremely hot as the prints become larger or faster, and the resulting parts can be vulnerable to deforming or cracking.
The new printer, however, vertically prints a nonstick liquid that cures as it moves over a window projecting ultraviolet light. The window, engineers added, removes much of the heat from the process before moving the part through a cooling unit.
The material’s nonstick properties, in particular, increase the printer’s speed 100-fold by eliminating the need for removing parts from the system. The components also do not require additional finishing, such as sanding or machining.
Northwestern engineers said the system could finally enable companies to bypass expensive injection molding systems — and storage space for excess parts — in favor of on-demand production.
“When you can print fast and large, it can really change the way we think about manufacturing,” Northwestern chemist Chad Mirkin said in a release.