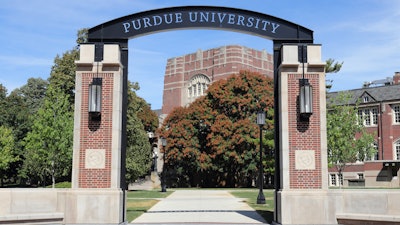
WEST LAFAYETTE, Ind. — Purdue University material engineers have created a patent-pending process to develop ultrahigh-strength aluminum alloys that are suitable for additive manufacturing because of their plastic deformability.
Haiyan Wang and Xinghang Zhang lead a team that has introduced transition metals cobalt, iron, nickel and titanium into aluminum via nanoscale, laminated, deformable intermetallics. Wang is the Basil S. Turner Professor of Engineering and Zhang is a professor in Purdue’s School of Materials Engineering. Anyu Shang, a materials engineering graduate student, completes the team.
Wang and Zhang disclosed the innovation to the Purdue Innovates Office of Technology Commercialization, which has applied for a patent from the U.S. Patent and Trademark Office to protect the intellectual property.
The research has been published in the peer-reviewed journal Nature Communications. The National Science Foundation and the U.S. Office of Naval Research provided support for this work.
Lightweight, high-strength aluminum alloys are used in industries from aerospace to automobile manufacturing.
A traditional method to alleviate hot cracking during additive manufacturing is the introduction of particles that strengthen aluminum alloys by impeding the movements of dislocations.
The Purdue researchers have produced intermetallics-strengthened additive aluminum alloys by using several transition metals including cobalt, iron, nickel and titanium. Shang said these metals traditionally have been largely avoided in the manufacture of aluminum alloys.
The research team has conducted macroscale compression tests, micropillar compression tests and post-deformation analysis on the Purdue-created aluminum alloys.