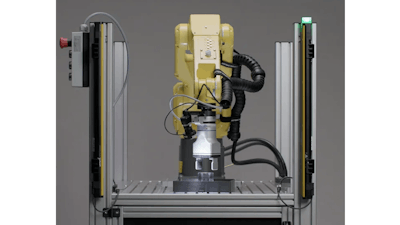
AI vision system vendor Micropsi Industries will showcase reflective disk picking and hook hanging applications at ATX West in Anaheim February 6-9. Too complex to automate with traditional programming, these applications represent the solutions the company can solve with its MIRAI system.
To continuously develop new solutions such as these, the company has established a new application laboratory in Magdeburg, Germany, in collaboration with its technology and research partner, the Fraunhofer Institute for Factory Operation and Automation (IFF).
MIRAI allows robotic arms to be controlled in real time, in direct response to sensor information taught by human demonstration. The reflective disk picking demo, shown in booth 4566 with a FANUC LR Mate industrial robot, will highlight the software’s ability to enable the robot to adapt to environmental variances and interact with reflective surfaces and extreme lighting conditions in real time.
The hook hanging demo, with a UR10e collaborative robot, highlights how MIRAI can deal with the positional variances of its target object by using all degrees of freedom to meet the target in 3D space.
Experts from Micropsi Industries and Fraunhofer IFF collaborate closely to explore and implement entirely new solutions in industrial robotics. The main focus of the lab includes:
- Feasibility studies and innovative approaches: using Micropsi Industries' AI-based vision system, MIRAI, the partners explore and test novel robot applications. MIRAI enables robots to dynamically adjust to workspace changes and handle tasks previously deemed too complex to be automated. Solutions for specific applications are developed through feasibility studies that aim to create new benchmarks in industrial robotics and inspire industry stakeholders to adopt new automation solutions.
- Tailored and complex automation challenges: manufacturing companies can present their specific automation challenges to the use case lab. Through close collaboration, the application is developed for the first time, accompanied by comprehensive instructions that allow customers to replicate the final robotic solution. These instructions will eventually be made available to a wide audience, fostering knowledge transfer within the industry.
The partners have already completed their first project: a dual in-line memory module (DIMM)-insertion task using a FANUC LR 10 robot augmented by the AI-powered MIRAI vision system. The DIMM task is complex because the robot is expected to precisely insert modules into delicate slots on a motherboard that varies in its position in the workspace.