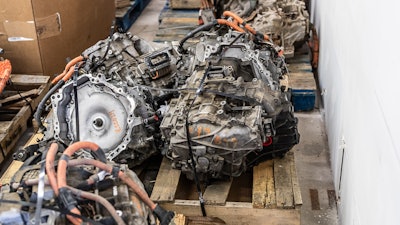
Advanced metals recycling company Cyclic Materials announced successful results from its new Kingston, Ontario pilot plant, where its proprietary Mag-Xtract technology isolates magnets from recycled end-of-life products. The design capacity of the plant is 1,000 kg/hour (8,000 tons per year), and initial runs have processed several tonnes of magnet feedstock per day.
“The launch of our pilot plant is a major step forward for developing a domestic, circular supply chain for critical materials at the scale needed to support the clean energy transition and technological innovation,” said Ahmad Ghahreman, co-founder and CEO of Cyclic Materials. “Our magnet-agnostic recycling technology produces one of the cleanest and highest quality mixed rare earth oxide products available on the global market—an environmentally sustainable, first-of-its-kind solution to the limited international supply of critical magnet materials.”
In 2022, Cyclic Materials completed an initial proof-of-concept of Mag-Xtract, processing 4000 kg of magnet-containing products—including copper, aluminum and steel— from end-of-life products. These materials are critical to the development of electric vehicles, wind turbines, smartphones and other technologies. In addition to developing Mag-Xtract, Cyclic Materials is scaling its proprietary hydrometallurgy technology to convert magnet feedstock and manufacturing waste into mixed rare earth oxide, cobalt-nickel hydroxide, and other by-products. Last fall, Cyclic Materials piloted its hydrometallurgy technology at a capacity of 10 tonnes/year. It is currently developing the first commercial demonstration plant for this technology in Kingston, ON, with a target launch date in Q2 2024.
Cyclic Materials investors include BMW iVentures, Energy Impact Partners, Planetary Capital, Fifth Wall and Bio-industrial Innovation Canada, totaling over USD $30 million in funding raised to develop its advanced metals recycling processes. The company has also received a CAD $3.6 million (USD $2.6 million) grant from Sustainable Technology Development Canada (SDTC).