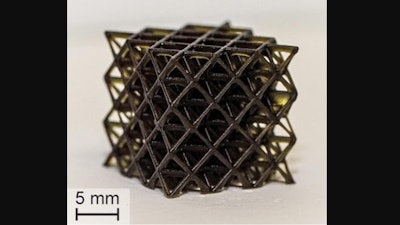
3D printing has driven innovations in fields ranging from art to aerospace to medicine. However, the high-energy ultraviolet (UV) light used in most 3D printers to cure liquid resins into solid objects limits the technique's applications. Visible-light curing, which would be more appropriate for some uses, such as tissue engineering and soft robotics, is slow. Now, researchers reporting in ACS Central Science have developed photopolymer resins that boost the speed of visible-light curing.
With the help of computer-aided design, 3D-printed objects are made by the successive layering of a material into a 3D shape, with each layer solidified or "cured" using UV light. Being able to use visible light for curing would have advantages, including reduced cost, improved biocompatibility, greater depth of light penetration and reduced light scattering. These attributes could open up new applications for 3D printing, such as making opaque composites, multi-material structures or hydrogels containing live cells. However, because visible light is lower in energy than UV, visible-light curing is currently too slow to be practical. Zachariah Page and colleagues wanted to find a way to speed up the process.
The researchers developed violet-, blue-, green- and red-colored resins that contained a monomer, a photoredox catalyst (PRC), two co-initiators and an opaquing agent. When the PRC absorbed visible light from LEDs, it catalyzed the transfer of electrons between the co-initiators, which generated radicals that caused the monomer to polymerize. The opaquing agent helped confine curing to the areas struck by light, which improved spatial resolution. The optimized mix of components allowed the researchers to print stiff and soft objects with small features (less than 100 μm), mechanical uniformity and build speeds up to 1.8 inches per hour. Although the best build speed is still less than half that of the fastest rate obtained using UV light, it could be further improved by increasing the light intensity or adding other components to the resin, the researchers say.
The authors acknowledge funding from the U.S. Department of Defense and the Welch Foundation.