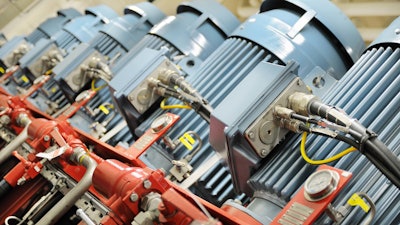
According to an ARC strategy study, 58 percent of manufacturers surveyed have no formal plans to manage the lifecycle of their technology. But, when unexpected breakdowns happen, opting for a brand-new device isn’t always the sensible option. Here's some insight on how sourcing Eco Obsolete Technology (EOT) could help keep automation processes running, without compromising on efficiency.
Improving energy efficiency is a common objective of manufacturers, with many joining the U.S. Department of Energy’s (DOE) Better Plants program. As a voluntary partnership initiative to promote energy efficiency in manufacturing facilities, the scheme’s partners commit to long-term energy efficiency goals — typically 25 percent savings over a span of 10 years.
According to the program’s most recent report, partners have reportedly estimated cumulative energy savings of 1.06 quadrillion British Thermal Units (Btu). In terms of energy cost savings, this translates to roughly $5.3 billion.
With the potential of significant financial gains, many manufacturers are opting for the adoption and implementation of cutting-edge technologies to improve efficiency. But, the reality is this, if facilities were upgraded every time new components were released, manufacturers would be bankrupt before the parts were unpacked from their boxes.
How do manufacturers strike the balance? How can facilities achieve energy efficiency objectives, without splurging on the latest equipment? Sourcing Eco Obsolete Technology (EOT) is one cost-saving answer.
EOT describes technology which, despite no longer being produced by the original equipment manufacturer (OEM), either because demand has dropped too low, or because the technologies to produce it are no longer available, still complies with current energy efficiency standards. Therefore, the parts can continue to be used efficiently in manufacturing environments.
Although EOT automation parts may no longer be available for purchase from the OEM, these pieces of equipment will most likely still exist in the stock of parts suppliers — at a much lower price point. Consider a Human Machine Interface (HMI) as an example.
Simply put, a HMI is the device that makes human-to-machine communication possible. Usually, HMIs are computerized and use an interactive display screen to show variable program data, system messages and operator messages. HMI manufacturers are almost constantly developing new versions to keep up with user demands, such as improved visualization and better energy efficiency. As a result, HMIs of only a few tears old can be discontinued by the manufacturer. However, this doesn’t mean older HMIs are rendered useless.
Many organizations rely on older or obsolete HMIs to keep operations running, especially for those who cannot afford costly production downtime. But what if an older HMI doesn’t meet the efficiency needs of the facility? In this instance, plant managers should seek out an EOT HMI. This could mean replacing a broken HMI with an identical one. Regardless of the age of the equipment, this could be possible by sourcing it from an obsolete parts supplier. This is especially beneficial if it has already met the energy efficiency needs of the plant and the staff were happy with it.
Alternatively, the plant manager could obtain another EOT HMI from an industrial parts supplier. Good suppliers, like EU Automation, will have an extensive network of industrial automation contacts to source parts from. With access to a wide global marketplace, finding an energy efficient and budget-friendly HMI won’t be a problem.
Energy efficient automation parts are still widely used in industry because they remain just as relevant and effective today as they were when they were first manufactured. By embracing EOT, manufacturers can become more energy efficient, in keeping with the efficiency goals laid out by the Better Plants Program.