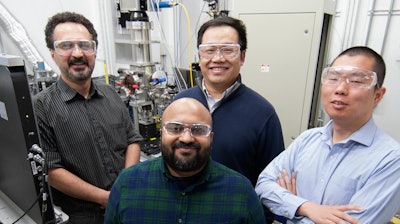
High-powered x-rays at a Chicago-area federal research facility provided unprecedented insight into the 3D-printing process — and could lead to stronger, more consistent printed parts.
Researchers from the Argonne National Laboratory and Carnegie Mellon University used the bright, high-energy x-rays to take high-speed video and photos of the Laser Powder Bed Fusion additive manufacturing technique.
The LPBF process uses lasers to melt and fuse powders into a printed part, but scientists said the method can trap tiny pockets in the material and weaken the finished product. The Argonne x-rays — some of the most powerful in the world — were able to shine a light, for the first time, on how the tiny cavities known as “vapor depressions” form.
“For additive manufacturing to really take off for the majority of companies, we need to improve the consistency of the finished products,” said Carnegie Mellon engineer Anthony Rollett. “This research is a major step in that direction.”
The x-rays allowed scientists to view how a laser moves across the bed of metal powder. The research, published in the journal Science, showed that the laser can result in a larger pool of melted metal than anticipated, which researchers named the “keyhole phenomenon” due to the shape of the larger pool.
The study also found that the “keyholes” can occur in practically all printing conditions — a reflection of the importance of the laser focus during the printing process.
More importantly, engineers used the research to create a method of predicting when they could form. Implementing that knowledge, they said, could one day lead to faster 3D printers producing more durable parts.
“It takes hours to print a part that is a few inches high,” Rollett noted. “That’s OK if you can afford to pay for the technique, but we need to do better.”