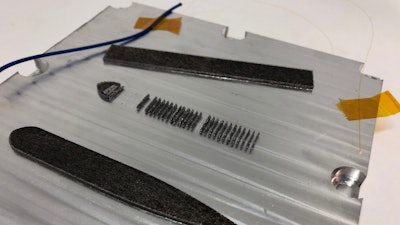
Fabrisonic’s patented low-temperature Ultrasonic Additive Manufacturing (UAM) process utilizes ultrasonic welding to 3D print metal parts. Although our process does not use powders, we have lots of friends in industry that use powder-based processes. One of the biggest complaints we hear from our powder brethren is consternation around build plates:
- Parts can debond or delaminate from the build plate during printing, which can be difficult to detect since the part is buried in powder.
- Build plates distort due to built-up residual stress.
- Build plate bolts break from excess residual stress during a build.
- We don’t understand how stress builds up around individual parts during a build leading to distorted final parts.
During one such conversation with our colleague at EWI, he asked, “How can we measure the loads going through the build plate?” Since Fabrisonic was working currently on embedding strain sensors in aerospace parts, we suggested that we 3D print a build plate with embedded sensors. And thus began the journey to build a "smart baseplate" or "smart build plate."
Fabrisonic teamed with EWI (PBF research) and Luna Innovations (fiberoptic sensors) to design and build an instrumented PBF build plate for the Defense Logistics Agency (DLA) under a Phase I STTR. Fabrisonic used its solid-state 3D process to print a plate with a single embedded fiber optic sensor. The fiberoptic was embedded with a specific undulating pattern that allows resolving the strain across the entire build plate. The team put the smart baseplate in EWI’s PBF machine and attempted a build that included "problematic" features. From this initial build, the team found that the device picked up significantly more information than just bulk stress state:
- Resolution and scan rate were high enough to actually discern the scan strategy of each layer.
- Defects showed up as large compressive strains forming early in the build at localized points.
- Slow delamination of a specific feature could be seen in the data although the recoater blade never hit the build.
The video above shows true strain-time plots resolved in the x-y plane (left) and the raw data along the length of the fiber (right). These colorful strain-time histories easily communicate what is happening in the build. However, further data slicing can provide a deep understanding of the quality of the build:
- Analyzing individual "pixels" for sudden vector changes provides tell-tale signs of many build issues.
- Comparing time histories of adjacent pixels also highlights problems in the build.
Figure 1 – As a crack forms and propagates it is normal to see a transverse compression to form at the point of separation (left). Strain vector changes also highlight certain flaws (right).
Based on the preliminary results, the team feels that this approach could be used to monitor quality during PBF builds:
- For series production, data can be compared between a known "good" baseline and subsequent serial numbers.
- For low volume, build flaws can be identified as they happen, allowing the operator to do a full abort, saving powder and machine time.
- For multi-part builds, build flaws in a single part can be seen, allowing the operator to abort that feature before it affects others.
The team has recently been awarded a PH II STTR with the DLA to further explore this technology. We hope to expand the capabilities by refining data mining techniques and embedding more sensors. For instance, by embedding sensing fibers at two heights, we can resolve both planar stress and movements.
Mark Norfolk is the president and CEO of Fabrisonic.