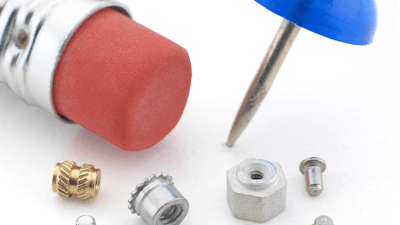
Compact consumer electronic devices can present outsized challenges when deciding how best to attach components and assemblies. The demands of size, durability, limited footprints, fast-changing technology, and the drive to control costs for hardware have been among the typical attachment issues involving end products ranging from wearables (smart watches, cameras, fitness bands, and headphones) to eReaders, tablets, and all innovations in between. Entire families of micro fasteners — threaded and unthreaded — introduce practical solutions.
The number and types of micro fasteners have expanded in response to the many evolving applications where their specification will make sense. Some micro fasteners in today’s marketplace rely upon self-clinching fastener technology, where the fastener becomes a permanent and integral part of a thin metal assembly. Other types are designed for installation in plastics and printed circuit boards. Micro fasteners already are serving in a wide range of applications and many types can be installed automatically in high volumes as typically required to promote cost-effective and timely production. An overview:
Threaded self-clinching micro standoffs mount and/or space components in applications with extremely limited real estate for attachment hardware. Standard types have been developed with threads as small as M1 / #0-80 and in lengths as short as 2 mm / .080”.
Threaded micro flaring standoffs attach permanently in any panel as thin as 0.2 mm / .008” of any hardness, including metal or stainless steel, plastics, and printed circuit boards. The flaring feature allows for installation into multiple panels and enables reduced centerline-to-edge designs. Threads are as small as M1 / #0-80.
Unthreaded self-clinching micro pins ideally suit locating, positioning, and/or alignment applications in stainless steel assemblies. Standard versions are designed with diameters as small as 1 mm / .040” and in lengths as short as 2 mm / .080”. The pin’s head mounts flush into stainless steel panels and these fasteners will exhibit excellent corrosion resistance.
Threaded self-clinching micro tack screws enable cost-effective sheet-to-sheet attachment by simply pressing them into place in aluminum or stainless steel sheets. (Top sheets can be made from any material.) As viable alternatives to screws, these stainless-steel fasteners avoid various screw-related issues, including costly tapping, cross-threading, torque control, and vibration back out, and can be removed easily by unscrewing (allowing for disassembly).
Unthreaded micro tack pins will accommodate those sheet-to-sheet attachment applications where disassembly will not be required. The aluminum or stainless steel pins can install in either aluminum or stainless steel sheets and the top sheet can be made from any material. An interference fit minimizes installation hole tolerance issues, a tapered tip assists location, and a low-profile head saves space.
Unthreaded broaching micro pins can attach top panels of any material securely to a base panel or chassis manufactured from common magnesium die-cast materials (such as AZ91D) or plastics (such as ABS). From a design perspective, their unique diagonal knurl effectively holds the top panel to a base panel or chassis by broaching into the base panel/chassis using a simple press-in action without requiring heat or ultrasonic operations.
Thru-threaded micro inserts for plastics will install (using ultrasonic equipment or a thermal press) either in straight or tapered mounting holes. Their symmetrical design saves time during production by eliminating any need for orienting the fastener prior to installation. The brass or lead-free inserts can be specified in thread sizes as small as M1 / #0-80 and in a variety of lengths.
Threaded surface-mount micro spacers for printed circuit boards have been engineered for nut and spacer applications on boards. They install permanently (in the same way and at the same time as other board components) and can be supplied in thread sizes as small as M1 / #0-80 and lengths as short as 1 mm / 0.62”. Ultimately, the spacers eliminate a need to place hardware manually on a populated printed circuit board.
From a purely design and engineering perspective, extremely small micro fasteners are in a world of their own and are not simply scaled-down versions of larger counterparts. When fasteners are downsized to lengths as short as 1 mm, thread sizes as small as M0.8, and diameters under 1 mm, issues relating to tight tolerances and performance values, among others, become magnified. Unique features engineered into a micro fastener become both critical and essential with specialty design coming into play.
This engineering underscores the inherent benefits in partnering with an experienced fastener supplier ideally equipped to manufacture and deliver precision parts, provide the requisite engineering know-how and support for application success, and innovate with custom fastener solutions for next-generation application challenges.
Jay McKenna is Global Business Manager-microPEM Fasteners at PennEngineering.