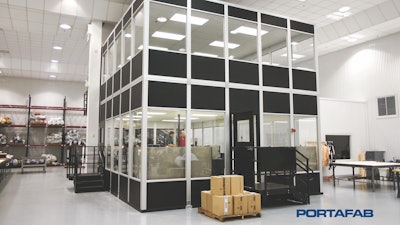
With ever rising costs and shortages in the construction labor market, more and more companies are exploring modular building systems to create warehouse office space, cleanrooms and other interior structures as an alternative to traditional, stick-built construction. While the market for modular wall systems has been around for decades, manufacturing facility managers are now using modular systems to build significantly larger structures to take advantage of huge labor savings and faster construction times.
“The labor savings achieved with modular construction extend throughout every aspect of the project," PortaFab President Wayne McGee said. "Modular building systems require less design and engineering time, streamlined installation (instead of complex onsite construction with multiple tradespeople) and minimal cleanup. When you add in the time and labor involved in coordinating all the trades required in traditional construction – the overall labor costs associated are huge.”
Here are four ways in which modular construction saves on labor.
3-piece stud systems provide customers with the added ability to install buildings very quickly while easily integrating electric, data and other cabling.PortaFab
1. Reduced Design & Engineering Time
First, modular building systems require less time for design and engineering. All pre-engineered components integrate seamlessly and include everything from the framing system to wall panels, roof and ceiling options, windows, doors, electrical and more. In addition to endless configurations and possibilities, modular construction offers the assurance of time-tested design and engineering that was made to work together from its inception.
With CAD drawings and full specifications available for all building components, structural calculations are also greatly simplified. This process can historically be time consuming and expensive as the sheer volume of work is substantial for stick-built projects. CAD drawings are also available and ready to download for easy integration into a construction RFP or use for implementation on site depending on the size of one’s project.
2. Streamlined Installation vs. Onsite Construction
Next, because modular building systems feature pre-engineered components manufactured in greater volumes in a highly controlled environment, they can be produced more quickly and with more consistent quality. Most modular building systems feature post-and-panel designs that utilize standard components that fit together quickly and easily. Assembly requires very few tools and less skilled labor than traditional construction.
The need for less-skilled labor also helps contribute to the labor savings of the overall project. Typical stick-built construction requires more highly experienced and multi-skilled craftsmen that are in higher demand and not even available in all regions of the country. In contrast, modular systems are essentially constructed on high-volume, automated production lines.
3. Minimal Clean Up
Third, modular building systems reduce waste, scrap and the dust associated with cutting and fabricating all of the components. The components are built off site and integrated and installed without saw dust or dry wall, paints, insulation, etc. There is no need to send extra components in case one makes a bad cut or measures something incorrectly. Modular systems are typically delivered in one shipment with all the components and can be quickly transported to the installation area for installation. Cleanup typically just includes disposal of the packaging materials.
In contrast, extensive labor is often required to clean up before, during and after a traditional construction project – which often requires many more days than a modular construction project. This daily debris clean-up alone can require a lengthy coordination effort to minimize disruption to the operation.
Many modular offices and buildings can be outfitted with modular electrical systems that further reduce the need for highly skilled electricians.PortaFab
4. Coordination of Trades
As a final point, modular building systems simplify the coordination of the people involved in a typical construction project. Not just the architects and specifiers, but the in-house production of all the building components virtually eliminates the need to coordinate carpenters, drywallers, painters, etc.
In summary, while there are many benefits to building with modular systems, the labor savings are really resonating with customers these days as the construction industry deal with a shortage of skilled labor.