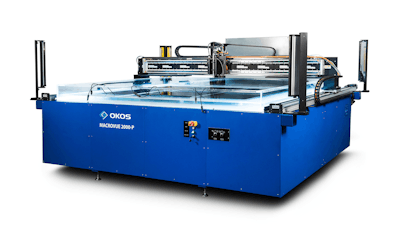
For the battery manufacturers powering the exponential growth of sectors such as electric vehicles and battery energy storage systems, testing various components for flaws before shipping is crucial to prevent potentially serious safety and performance issues. The need is only expected to increase, as production volumes ramp up.
The global battery market is expected to expand at a compound annual growth rate of 15.8% from 2023 to 2030, with lithium-ion batteries gaining most of the market share by 2024, according to Grand View Research.
When manufacturing battery cells, various defects can occur that require detection so the product can be removed before shipping. Microscopic cracks can occur in the electrode materials or the separator, potentially leading to reduced performance and safety concerns. Inconsistent coating on electrodes can lead to short circuits or reduced capacity.
Gaps between layers in a battery cell, such as the separator and electrodes, can result in uneven charge distribution and potential thermal issues. Delamination between layers of materials within a cell can compromise its structural integrity.
Inadequate battery inspection can pose serious dangers. Certain defects, especially those that lead to internal short circuits, can result in safety risks like overheating, fires or even explosions. Additionally, defects can cause a decrease in battery capacity, efficiency and overall performance. Insufficient battery inspection may also lead to costly product recalls and damage the reputation of the manufacturer.
The need to assure quality is driving the adoption of non-destructive battery inspection techniques such as Scanning Acoustic Microscopy, which can provide more detailed insights into the internal structure of battery cells to identify cracks, defects, separations and delamination in the materials.
Scanning Acoustic Microscopy, acknowledged for its capability to identify defects as minuscule as 50-microns, is extensively embraced in the semiconductor industry as a metrology technology for failure analysis and reliability detection. Now the same high-speed technology is being applied to testing and failure analysis of battery cells.
With battery production booming, manufacturers are increasingly integrating Scanning Acoustic Microscopy inspection tools into their processes to catch defects at an early stage. For high volume operations, automated systems are also available that enable 100% inspection of battery cells, ensuring both safety and optimal performance.
SAM can detect defects in batteries as miniscule as 50-microns.OKOS
Scanning Acoustic Microscopy
Scanning Acoustic Microscopy (SAM) is a non-invasive, non-destructive ultrasonic testing method that works by directing focused sound from a transducer at a small point on a target object.
“The sound hitting the object is either scattered, absorbed, reflected or transmitted. By detecting the direction of scattered pulses as well as the ‘time of flight,’ the presence of a boundary or object can be determined as well as its distance,” explained Hari Polu, President of OKOS, a Virginia-based manufacturer of SAM and industrial ultrasonic non-destructive (NDT) systems. OKOS is a wholly owned subsidiary of PVA TePla AG, Germany and offers both manual and automated inspection systems for flat panels, thin plates, circular discs, sputtering targets and special alloys.
Polu notes that samples are scanned point by point and line by line to produce an image. Scanning modes range from single layer views to tray scans and cross-sections. Multi-layer scans can include up to 50 independent layers.
“Depth-specific information can be extracted and applied to create two- and three-dimensional images without the need for time-consuming tomographic scan procedures and more costly X-rays. The images are then analyzed to detect and characterize flaws such as cracks, inclusions and voids,” said Polu.
With the rising demand for batteries in the market, there is now a need for an automated method to inspect all batteries during the manufacturing process. The challenge, however, is performing 100% inspection at sufficient throughput speeds to remove materials with defects that do not meet strict quality requirements. As with other inspection systems, increasing scanning speed traditionally meant sacrificing scanning image resolution.
Fortunately, recent advancements in SAM technology have significantly improved throughput speeds and defect detectability.
“While a conventional 5 MHz sensor could take up to 45 minutes to inspect [a battery’s components], an advanced phased array with 64-128 sensors and innovative software to render the images reduces inspection time to five minutes with more granular detection of small impurities or defects,” said Polu.
By dramatically increasing inspection speed, Polu says the battery industry is no longer limited to selective sample testing during In-Process Quality Control. Although SAM has long been utilized for this type of inspection, the testing involved a handheld unit or a multi-point inspection. Now it is more feasible to conduct 100% inspection of the entire surface/interface.
In addition, these advances also facilitate the detection of not just gross defects, but much smaller defects, to drive highly consistent, high yield products.
Battery manufacturers are increasingly integrating SAM inspection tools into their process to catch defects at an early stage.OKOS
“Advanced, phased array SAM systems make it possible for battery manufacturers to move to a higher level of failure analysis because of the level of detection and precision involved,” said Polu. “In the past, detecting a 500-micron defect was the goal; now it is a 50-micron defect. And with batteries integral to increasingly important products like electric vehicles and battery energy storage systems, they want to inspect every item, not just a few samples.”
When high throughput is required for 100% inspection, ultra-fast single or dual gantry scanning systems are utilized along with 128 sensors for phased array scanning. Multiple transducers can also be used to simultaneously scan for higher throughput. “In tests, the equipment can now scan batteries over ten times faster,” said Polu.
As important as the physical and mechanical aspects of conducting a scan, the software is critical to improving the resolution and analyzing the information to produce detailed scans. Multi-axis scan options enable A, B and C-scans, contour following, off-line analysis and virtual rescanning for batteries, which result in highly accurate internal and external inspection for defects via the inspection software.
“OKOS decided early on to deliver a software-driven, ecosystem-based solution,” said Polu. The company’s ODIS Acoustic Microscopy software supports a wide range of transducer frequencies from 2.25 to 230 MHz.
Polu estimates that the company’s software-driven model enables them to drive down the costs of SAM testing while delivering higher quality inspection results at faster speeds.
“With more sensors and advanced software to interpret the information at very high resolutions, battery OEMs can inspect 100% of the materials utilized at a level one to two orders of magnitude better to discover flaws that were previously undetected. This will increasingly become the industry’s best-in-class standard,” concluded Polu.