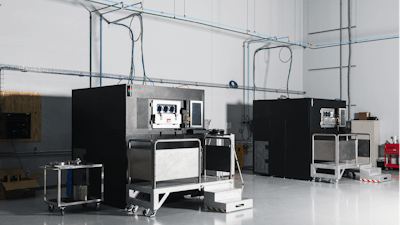
I don't know how you run a metal additive manufacturing (AM) shop without a strong CNC shop. Many of my colleagues in the AM and related machining community would likely agree, defining workplace integration as the sharing of information between 3D printers, CNC machinery, the software systems needed to program them, and the design tools used to develop and optimize the final products.
That's part of it, but in my experience integration goes even deeper, requiring targeted, pre-manufacturing planning and smart, well-structured workflows. That's what's different about working in AMāthe amount of upfront engineering needed compared to traditional manufacturing. Most of your additive work occurs in the engineering stage as opposed to the actual production stage, so itās very heavy on the front-end to drive that integrated workflow.
Nearly everything we manufacture in metal additive requires some sort of machining, whether that's tapping threads, machining interfaces, or smoothing surfaces for finish or tight tolerances. Integrating metal printers with traditional CNC equipment is a far-reaching value driver for our customers, in that it helps reduce supply chain costs and vendor management issues and cost. One of our team members likes to call it the āone neck to wringā principle.
Achieving this level of responsibility means tight control over every step in the process. This begins with providing customers with the engineering and manufacturing advice needed for a successful design and carries through to delivery of the finished product.
A Velo3D Sapphire AM system at ADDMAN.Image courtesy of ADDMAN
Many in this industry place too much of their focus on just delivering that print job, but thereās a lot more to it than that. AM parts need to be produced in their entiretyāwhich includes any required secondaries such as heat treatments, post-processing, coatings, non-destructive testing, and more. What on-site CNC allows you to do in terms of support structures, surface finishing, etc., is a game changer. You arenāt making paperweights, right? You want something that's fully functional, meets engineering requirements, and doesnāt just ālook likeā what the customer wants. The final material properties, which make or break a part, are developed in the process so there needs to be a robust understanding of how all variables of the process impact the output.
As I noted at the outset, integration of all AM-associated processes is critical, along with making certain your 3D-printersā design, build, and programming software platforms communicate with each other. Once youāve got your base process established, repeatability is key. Itās for this reason, among some others, that we recently added to our fleet of two dozen or so printers by investing in a pair of high-capacity, advanced metal AM systems that prioritize these attributes.
Our customers asked us to acquire these machines; many of them get involved early by telling us up front what they want to see in a printer. It's a two-way conversation, but oftentimes itās the customer leading it. These days many of their requirements are being met by the qualification package that comes with our newest systemsā software platforms and extremely strict process controls, which together provide the degree of repeatability across multiple machines thatās required to ensure validation.
Iām not at liberty to say which OEMs weāre working with, but many of them make rockets, so if these types of organizations both endorse and stipulate the use of certain advanced AM systems and software, it underscores the correctness of our equipment selection.
With the manufacturing and design teams (including the customerās) in sync, itās nice to think weāre all part of a mature, fully developed additive manufacturing industryā but weāre not there yet. In fact, a majority of parts made today will see some degree of redesign based on the technology used to produce them. And while the more-advanced AM systems weāre now working with have opened up a significantly broader design space for us, that success still stems from adhering to the rules of physics that determine optimum AM-component performance.
Just as one wouldnāt design a workpiece for a milling operation and then attempt to turn it on a lathe, each AM process has its own set of unique design considerations. Unfortunately, the knowledge of designing for specific manufacturing processesāAM and otherwiseāis not commonplace among many designers and engineers. Itās therefore crucial that we and other manufacturers help customers develop the most effective designāone compatible with the production quantities, desired price-point, and intended manufacturing technologyāand then provide the fastest, most cost-effective means of manufacturing their product.
Technicians operating a Velo3D Sapphire AM system at ADDMAN.Image courtesy of ADDMAN
Vertical integration helps with all of this, particularly in the case of AM. Within our company, we're not reliant on our vendors' schedules. We can run jobs as needed and adjust as parts come out of the printer and head off to heat-treat, the machine shop, or one of our sister companies. Having that ability to flex our workflow is a huge benefit.
But part of being successful in todayās blend of additive and subtractive manufacturing relies on what I like to call the cross-pollination of knowledge between machinists and additive engineers. Together these teams can decide on strategies that improve downstream processing, such as adding stock in strategic places and integrating fixturing. Doing so makes the parts easier to machine and helps to cut costs, especially where higher production volumes are concerned. And in AM workpieces with complex features like thin walls or hard-to-reach areas, this collaboration can substantially reduce scrap rates and eliminate the āgotcha momentsā that might otherwise occur long after a build and expensive processing is complete.
The more advanced AM systems have helped considerably in this regard. Their ability to produce low-angle and horizontal surfaces with fewer or sometimes no supportsāas well as greater part consistency and the use of validated, high-quality materials that provide more predictable resultsāhas made machining much simpler than it once was. As a result, weāve achieved a great deal of confidence in our processāand many of the 3D-printed parts weāve made are in space right now.
Key to reaching such achievement is understanding a customerās value drivers from the start, and delivering the best possible products based on those goals. That means assisting them in assessing variables such as production volume, manufacturing costs, material selection, and the most suitable production methodāwhether thatās pure additive manufacturing, CNC machining, a hybrid approach, or modifying their designs and combining assemblies to fit within the various constraints.
AM is definitely part of the manufacturing mix these days, but it does remain a relatively young industry. Weāre likely still going to be spinning our wheels on standards and qualifications for the next few years, but a decade from now? Where appropriate, additive manufacturing, backed by robust and integrated CNC machining technology, will rule. When we look at large-scale production, AM is going up against casting, which has been done since almost the beginning of mankind. But recent supply chain hiccups have highlighted AMās faster turnaround times and distributed manufacturing potential. So AM is already on its way; we just need to get past any remaining production bumps and work with regulators to establish more of the material qualification pieces.
Here's the current reality: darn near every commercial rocket that goes up these days is being propelled by an engine that's made almost fully of additive. This stuff is proven and weāre making fantastic progress; it just needs to be a little more ubiquitous. I'd like to see better collaboration around data. I think there are a lot of companies doing very, very similar things, and we need to get some of that out in the open in order to dispel the remaining questions. We need to share and collaborate more. Once we do that, it will completely unleash AM's remarkable potential.