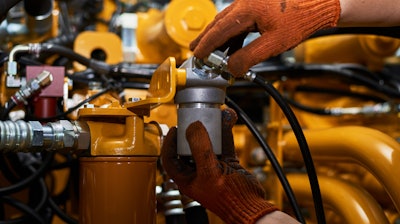
Hydraulic system design can be a tricky thing to get right, especially when people want to save energy. However, designers are much more likely to feel satisfied with the outcomes when they know which errors to avoid.
1. Using the Outside Diameter to Size Fluid Connectors
Flexible hoses, steel tubing and schedule piping are a hydraulic system's most common fluid connector types. In addition to using the proper fluid connectors, designers must choose the fittings that link tubes, hoses and pipes. The two primary purposes of these connectors are to hold and seal. Some of the earliest fluid connectors featured tapered threads, which required the use of chemical or pipe sealant.
People also use metal seal connectors. They resemble tapered thread connectors but include a 30-degree machined face, making this type better able to withstand the high pressures in hydraulic systems. More specifically, the machined face maintains the proper seal while the connector’s thread handles the holding.
The most recently developed hydraulic fluid connectors are soft-seal varieties. These components have synthetic or natural elastomeric seals to stop leaks. They typically have O-ring style seals, which are only compatible with specific temperatures and system fluid types. Thus, designers must only use soft-seal connectors after verifying compatibility. Metal and threaded connectors also require people to weld them to tubes if using the two together.
The Importance of Connector Diameter
Choosing the most appropriate fluid connectors and fittings is only the start of a successful hydraulic system design. Designers must also select the correct fluid connector diameter. An improper size could lead to leaks and other issues compromising energy efficiency. One common mistake in hydraulic system design is to select the connector’s size based on the conductor’s outside diameter. Doing that could cause flow turbulence due to friction between the fluid and the connector walls.
However, experts recommend sizing fluid connectors using the conductor’s inside diameter. As the inner diameter becomes smaller, fluid velocity increases. Manufacturers use the inner diameter when stating hydraulic system fluid connector size. Thus, relying on the outer diameter could make people design a system that doesn’t meet their expectations or requirements.
2. Failing to Understand the Impact of Individual Components on Efficiency
Some people underestimate how much single components can affect a hydraulic system’s overall efficiency. They may take a big-picture view rather than assessing how specific choices at every stage of the design process could help or hinder how well a system functions.
One company’s digital displacement pump technology reportedly enables a 15%–30% increase in efficiency. That change is due to a thoughtful pump design, advanced software controls and an electronic controller.
The pump selection is also an essential part of hydraulic system design, and the people involved must evaluate factors such as the pump’s size, operating speed and displacement. Moreover, variable displacement pumps are generally more efficient than fixed ones. That’s because fixed displacement pumps keep using energy when systems are still running but idle.
Conversely, variable displacement pumps only flow when the pump’s outlet pressure is less than its set pressure. Once it reaches the set pressure, the pump goes into a neutral state and does not begin producing flow again until its pressure drops.
An inverter drive can also make a hydraulic system more efficient because it allows manipulation of the motor and pump’s output speed. Some options can increase energy efficiency by 50% while reducing noise and emissions.
It’s even essential to scrutinize a hydraulic system’s piping. Removing unnecessary bends is a practical way to make the system’s fluid flow freely, boosting overall efficiency.
Although people should understand how various parts will work together to meet efficiency goals, they must recognize the impact of single components on efficiency. Keeping those specifics in mind is also helpful when a person wants to rebuild sections of a system to increase efficiency and get great results without starting from scratch.
3. Overlooking Ease of Maintenance in the Hydraulic System Design
If a hydraulic system is overly hard to maintain, some people may not perform upkeep as often as they should. Then, a hydraulic machine could become dangerous for operators or others in the vicinity.
For example, hydraulic cylinder drift is a problem where the cylinder moves down during operation. This issue can cause the cylinder to sink under heavy loads gradually. It also results in extra component strain, which could cause catastrophic failure during load-bearing tasks. Regular maintenance is the best strategy for preventing hydraulic cylinder drift.
More broadly, actuator leaks, cylinder friction and valve-related throttling losses are some of the many things that can cause energy-efficiency reductions in hydraulic systems. However, when people plan to help technicians maintain the machine through its life span, they greatly optimize its performance.
System wear and fluid contamination are two of the many things that can make hydraulics perform less reliably. Thus, many decision-makers have switched to predictive maintenance strategies that help them spot problems early rather than leaving them undiagnosed for too long. For example, old hydraulic fluid can make cylinders less responsive. However, predictive sensors can measure lubrication, cleanliness and overall quality, and flag signs of decreased performance.
Ensuring ease of maintenance in a hydraulic system design means making it simple for technicians to access specific components during diagnostics, upkeep and repair. That starts with providing ample room for the person’s hands and fingers and reducing the risk of crushing. Moreover, including cutouts or windows in the design is a straightforward way to improve monitoring between scheduled maintenance appointments.
Having a future-oriented mindset is also helpful. For example, how could designers make the hydraulic system easier to move when necessary? What aspects would simplify a future expansion?
Proactiveness Avoids Hydraulic System Design Mistakes
When a design team rushes through each phase or does not consider a client’s needs for a hydraulic system, mistakes, miscommunication and poor performance can result. However, carefully pondering each decision is an excellent way to create a highly efficient system that operates as intended for years to come.
Designers must take it upon themselves to weigh the pros and cons of every option and how it could affect overall efficiency. They should also study factors like price, component life span and ease of obtaining replacement parts. These things can indirectly affect efficiency by making upkeep as hassle-free as possible.
Emily Newton is the Editor-in-Chief of Revolutionized and an industrial writer who enjoys researching and writing about how technology impacts different industries.