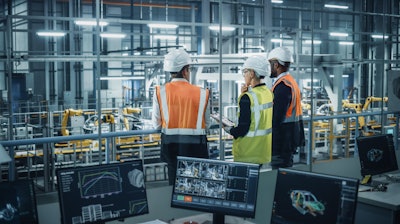
The manufacturing industry is continuously evolving to adapt to new technological advancements and changes in global markets. Industry 4.0, or the fourth industrial revolution (4IR), marks this evolution's latest stage.
It integrates cyber-physical systems, automation and data exchange in manufacturing processes. Such a blend of technology redefines manufacturing by driving unprecedented efficiency, innovation and customization.
Here's a quick overview of the manufacturing industry revolution:
- The first industrial revolution witnessed the rise of machines with water/steam power introduced to automate key aspects of the manufacturing process.
- The second industrial revolution led to mass production with assembly lines and electricity, allowing faster, more efficient manufacturing.
- Next, the third revolution leveraged computers and automation to improve production processes.
And currently, we are in the middle of the fourth industrial revolution, known as Industry 4.0, which began in 2011.
Industry 4.0 and the power of digital technology stack
This groundbreaking paradigm shift leverages the power of advanced technologies such as the Internet of Things (IoT), artificial intelligence (AI), robotics, quantum computing, CPQ software for manufacturing, 3D printing, big data analytics, etc. It can revolutionize production processes, supply chain management and operational efficiency.
Manufacturing businesses harness the potential of digital technology to drive unprecedented levels of automation, connectivity and data-driven decision-making. It fosters innovation, competitiveness and sustainable growth in the global economy.
Digital tech stack refers to the technology that modern businesses use to unlock 360-degree transformation. It can help industrial manufacturers develop better products using innovative software to enhance every facet of production.
Let's explore what the modern manufacturing digital tech stack looks like as businesses function amidst Industry 4.0.
1) CPQ (Configure, Price, Quote) Software
CPQ is one of the necessary steps for manufacturing businesses looking to go digital. It helps manufacturing businesses streamline their sales and product configuration processes.
This is done especially through creating quotes by ensuring all components and options are accounted for during product configuration.
It automates the quoting process, enhancing accuracy and speeding up customer delivery. Moreover, CPQ for manufacturing helps maintain price consistency across sales channels and localizes prices for various regions.
Integrating CPQ with other processes in Industry 4.0 can enhance efficiency, increase agility and improve customer satisfaction.
Here are some key strategies for using CPQ in manufacturing:
- Integrate your CPQ system with enterprise resource planning (ERP) and customer relationship management (CRM) solutions. This will enable seamless data flow between systems, improving accuracy and reducing manual work.
- Utilize IoT data since Industry 4.0 relies heavily on such technologies. Connecting CPQ systems with IoT devices can provide real-time data on product configurations, machine performance and product quality, enabling more accurate quotes and better decision-making.
- Collaborate with supply chain partners to facilitate communication and collaboration by integrating CPQ with supply chain management systems. This can optimize inventory levels, reduce lead times and improve responsiveness to customer demands.
- Adopt a cloud-based approach by using cloud-based CPQ solutions. It enables easier integration with other Industry 4.0 technologies, promotes scalability and facilitates real-time updates.
- Integrating CPQ with product lifecycle management (PLM) helps track products from design to end-of-life. This offers better configuration management and tracking of changes in product options and prices throughout the product life cycle.
2) Edge Computing
Edge computing refers to processing data near its source rather than sending it to a centralized data center or cloud. Here data is analyzed and processed at the "edge" of the network, closer to where it is generated, like in sensors or other devices. This helps manufacturing businesses reduce latency, lower bandwidth requirements and improve overall system performance.
In manufacturing, this technology is useful in real-time monitoring and control of equipment, predictive maintenance and quality assurance.
It enables seamless integration of IoT devices and Industry 4.0 technologies, resulting in better data-driven insights, increased automation and optimized resource allocation.
Here are some ways edge computing is useful for manufacturing companies:
- Edge computing offers real-time data processing by using sensors and equipment in real-time. This allows for faster decision-making and more efficient operations.
- Manufacturing businesses can use predictive maintenance by analyzing sensor data and identifying patterns. This way, edge computing predicts when equipment is likely to fail and recommends maintenance before a failure occurs to reduce downtime and extend the life of machinery.
- Data security is crucial when a manufacturing business takes strides on the digital front. Edge computing processes sensitive data on-site rather than sending it to a central data center to help protect against data breaches and ensure compliance with data privacy regulations.
- Manufacturing businesses also look forward to scalability. Here too, edge computing ensures easy infrastructure scalability by offloading some processing tasks to edge devices, reducing the burden on centralized systems.
3) Artificial Intelligence (AI) and Machine Learning (ML)
AI and ML are transforming the manufacturing industry by automating processes, improving efficiency and enabling predictive maintenance. AI-driven algorithms can analyze data collected from IoT devices and sensors, identify patterns and make data-driven decisions to optimize manufacturing processes.
Manufacturing businesses leverage AI and ML to improve efficiency, reduce costs, enhance product quality and drive innovation.
Here are some key applications of AI and ML:
- Predictive maintenance: AI and ML algorithms help analyze data from sensors and equipment to predict maintenance requirements, minimizing downtime and reducing maintenance costs.
- Quality control and inspection: Computer vision and deep learning are crucial tech stacks that automatically inspect products for defects. This ensures consistent quality and reduces the need for manual inspection.
- Demand forecasting: AI and ML can analyze historical data and external factors to predict future demand, helping businesses optimize inventory levels and production schedules.
- Supply chain optimization: Here, AI helps analyze and predict disruptions in the supply chain for businesses to make informed decisions on sourcing, logistics and inventory management.
- Robotic automation: AI-powered robots can perform repetitive tasks with increased precision and speed, freeing human workers for more complex and creative tasks.
4) Additive Manufacturing (3D Printing)
Additive manufacturing, commonly known as 3D printing, is another essential component of the modern manufacturing tech stack. It allows for the creation of complex parts and products using digital designs and materials.
3D Printing is a groundbreaking technology allowing manufacturing businesses to create complex, customizable, lightweight components with unparalleled precision and speed.
By building objects layer by layer, this method allows companies to design and produce parts that would be otherwise difficult or impossible to create using traditional manufacturing techniques.
Here are some of its key applications:
- Prototyping: Manufacturing businesses can use 3D printing in rapid prototyping to create prototypes cost-effectively. This allows for faster design iterations and reduced time to market.
- Customization and personalization: Additive manufacturing can help produce tailor-made products that cater to individual customer preferences, enhancing customer satisfaction and loyalty.
- Complex geometries: Manufacturing businesses can create intricate, lightweight structures with high strength-to-weight ratios that are impossible using conventional manufacturing methods.
- Tooling and molds: Additive manufacturing can produce tooling and molds for various industries, reducing lead times and lowering costs.
Bottomline
The future of manufacturing will heavily rely on businesses adopting technology tech stack. The growing competition requires manufacturing businesses to leverage various digital technologies. It helps modernize their processes, increases productivity and gives them an advantage in the global marketplace.
The manufacturing industry is on the cusp of a new age of innovation, productivity and sustainability thanks to the widespread adoption of a comprehensive digital technology stack like AI and ML, robotics and automation, 3D printing, CPQ, integration of advanced analytics and data visualization tools and much more. These technologies enable organizations to gain valuable insights from massive manufacturing-specific data.
---
Hazel Raoult is a freelance marketing writer and works with PRmention. She has 6-plus years of experience in writing about business, entrepreneurship, marketing and all things SaaS.