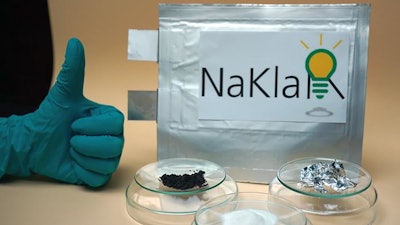
There is a promising alternative to conventional lithium-ion batteries, namely sodium-ion batteries. In these batteries, it is sodium ions instead of lithium ions that flow back and forth between the electrodes and in this way, store or release electrical energy.
Sodium-based batteries have a major advantage: unlike lithium, which is comparatively rare, sodium is available on earth in practically unlimited quantities. As a natural component of salt, it can be extracted from salt lakes or mines. In addition, sodium batteries do not require the equally rare metals cobalt and copper, which are essential for lithium batteries.
Interesting for Stationary Storage, but also Cars
Sodium batteries also have a disadvantage: their energy density is low. This means that they have to be larger, both in size and weight, in order to store the same amount of energy as a lithium-ion battery. Therefore, they are primarily suitable for applications where size and weight are not so important - for example, as stationary energy storage in houses with solar panels or as buffer storage to compensate for fluctuations in the power grid.
Nonetheless, sodium batteries are also interesting for electromobility. "They are suitable for smaller cars that are driven for shorter distances," says Dr. Guinevere Giffin, who heads a junior research group at the Chair of Chemical Technology of Material Synthesis at Julius-Maximilians-Universität (JMU) Würzburg in Bavaria, Germany.
Two Million Euros Funding From BMBF
Dr. Guinevere Giffin is coordinating the new project NaKlaR together with Professor Maik Finze from the Institute of Inorganic Chemistry (JMU). The project aims to make sodium batteries more efficient. The sustainability of is also to be further improved by optimising the production process and paying attention to the recyclability of the components right from the development stage.
The Federal Ministry of Education and Research (BMBF) is funding the project, over the Project Management Agency at Forschungszentrum Jülich (PTJ) with more than two million euros. In addition to JMU, the Karlsruhe Institute of Technology / Helmholtz Institute Ulm (Dr. Alberto Varzi) and the Fraunhofer Institute for Silicate Research ISC, Würzburg / Fraunhofer R&D Center for Electromobility FZEB (Dr. Simone Peters) are also involved in NaKlaR.
The project is supported by an industrial advisory board, which enables a regular exchange of information between the research organizations and industry. An industrial advisory board will closely follow the work, to advice on the interests and needs of industry throughout the research activities. The members of the advisory board include the companies E-lyte Innovations GmbH, Carl Padberg Zentrifugenbau (CEPA), CellCircle UG and Leclanché GmbH.
Batteries are Highly Complex Systems
The challenge that the project team is tackling is not trivial. "Batteries are very complex systems," says Dr Giffin. All components have to be very precisely tailored to each other to ensure a good performance, safety and lifetime.
One part of the work involves producing the battery electrodes as sustainably as possible. Currently, a toxic organic solvent is used to mix and coat the electrode components. The project team would like to replace this solvent with water – but this poses new challenges. Even small amounts of water remaining in the electrodes can cause problems in the battery cells.
Protecting Electrolytes and Active Materials from Water
New high-performance electrolytes must be developed that remain stable in the presence of water molecules. Electrolytes are the liquids which transport the lithium or sodium ions through the battery. The active materials responsible for storing energy in the battery must also be protected because they degrade in water, which significantly impairs the performance of the battery.
For active materials containing low value metals, as is the case with the sodium battery, a direct recycling process may be more profitable. The NaKlaR project is also specifically pursuing direct recycling. In contrast to lithium-ion batteries, where currently only the valuable metals are recycled, direct recycling preserves the active material in its original structure so that it can, in principle, be used directly for the production of new batteries.
Joint Project to be Funded for Three Years
The NaKlaR joint project was launched at the beginning of December 2023 and will run for three years. By the end of the project, the team aims to have developed a sodium battery based on protected cathode materials, aqueous production of the electrodes and hydrolysis-resistant electrolytes. At the same time, this battery should have a performance that is roughly equivalent to today's reference cells. Furthermore, the goal is to produce cells containing at least 25 percent recycled electrode material without any significant loss of performance.