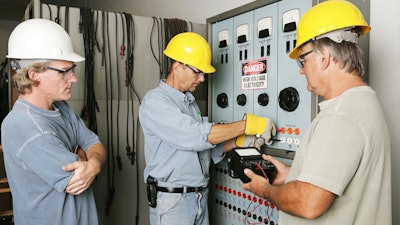
Despite preventing an estimated 120 fatalities and 50,000 injuries each year, lockout/tagout (LOTO) procedures account for one of the most cited OSHA violations each year. In 2019, the LOTO Standard 29 CFR 1910.147 “Control of Hazardous Energy” placed fourth in OSHA’s Top 10 List of most cited violations with 2,975 total violations; higher than the previous year. This standard outlines minimum performance requirements for the control of hazardous energy during servicing and maintenance of machines and equipment.
Employers cited under this standard failed to establish an energy control procedure either partially or altogether, while others were cited for failing to provide adequate employee training, failing to conduct periodic evaluations of procedures, and failing to use LOTO devices or equipment. Violations were common among plastics manufacturers, machine shops, and sawmills. Penalties for 2019 citations can cost as much as
$13,260 per violation and failure to act can lead to additional fines up to $13,260 per violation per day past the deadline to fix the issue.
Furthermore, failure to comply with OSHA citations can result in a $132,598 maximum penalty.
"2019 Annual Adjustments to OSHA Civil Penalties,” osha.gov.
At the National Safety Council 2019 Congress & Expo, Patrick Kapust, deputy director of OSHA’s Directorate of Enforcement Programs reported: “These are common violations that we’re finding – they’ve been in place for a lot of years. The answers are out there, and employers shouldn’t feel like these are very complex issues. If you don’t know the answers, we encourage you to contact OSHA.”
Since 2014, OSHA has issued employers more than 10,000 LOTO citations. In addition to the penalties paid for safety violations, preventable workplace incidents involving the release of stored energy cost companies millions in lost productivity, medical expenses, and insurance costs. With the available resources today, these completely preventable accidents and their associated costs should be on the downturn as opposed to 2019 seeing an increase in violations over the previous years. Employers are consistently failing upwards to comply with minimum performance requirements and it’s becoming more apparent that we’re far past the time for them to adopt Safety-By-Design solutions.
1) 878 Violations
1910.147(c)(4) Energy Control Procedure
Procedures shall be developed, documented and utilized for the control of potentially hazardous energy when employees are engaged in the activities covered by this section.
What makes compliance with the “minimum performance requirements for the control of hazardous energy” fall under the umbrella of common violations? To understand this, we need to start by defining the “LOTO” acronym. “Lockout” procedures refer to written steps that are taken to bring the machine to a zero energy state. Once a de-energized condition is established, locks are placed on energy isolation devices that enable personnel to maintain control over the hazardous energy. “Tagout” devices are only allowed as sole means for control of hazardous energy on machines/equipment that was made prior to January 2, 1990 where the equipment is not designed with provision to lock, although they do not provide any sort of control or protection other than warning personnel of the imminent hazard. They are meant to show that the equipment is in a de-energized state and someone is most likely performing maintenance on it.
When combined together, the procedure “lockout/tagout” refers to lockout devices and identification tags being used in conjunction to indicate that a qualified person is safely performing an energy isolated task. When employees follow the LOTO procedures enforced by the companies they work for, they are able to better protect themselves from unexpected re-energization or release of stored energy.
2) 878 Violations
1910.147(c)(7) Training & Communication
The employer shall provide training to ensure that the purpose and function of the energy control program are understood by employees and that the knowledge and skills required for the safe application, usage, and removal of the energy controls are acquired and demonstrated by employees, and documented by the employer.
When it comes to OSHA and LOTO, the code recognizes two categories of people that need training: Authorized & Affected Employees. Under the training mandated to companies by OSHA, “Each authorized employee shall receive training in the recognition of applicable hazardous energy sources, the type and magnitude of the energy available in the workplace, and the methods and means necessary for energy isolation and control. Each affected employee shall be instructed in the purpose and use of the energy control procedure.”
To summarize, “authorized employees” are those who are applying the locks and “affected employees” are those in the area during a lockout. The latter can range anywhere from operators to third-party contractors. If they are within the vicinity of the procedure, they are affected.
Ensuring that both authorized and affected employees have been trained is vital to a successful LOTO program.
While OSHA requires that all authorized and affected employees receive periodic training, the implemented training program at any organization can be customized to meet precise needs. However, companies training their employees to meet the minimum compliance standards does not result in achieving maximum safety and productivity.
Today, it’s possible for the implementation of a LOTO program to complement OSHA standards by enhancing compliance through the use of Permanent Electrical Safety Devices (PESDs). By installing PESDs wherever LOTO procedures are performed, companies can facilitate these additional safety measures into their written LOTO program to ensure even further reduced risk and increased productivity.
As evidenced by the record high LOTO violations of 2019, companies need to do more in 2020 to improve and ensure worker safety and really ask themselves if they’re investing in safety just to satisfy a compliance and avoid fines, or if they are investing in preventing injuries and saving lives.
3) 500 Violations
1910.147(c)(6) Periodic Inspection
The employer shall conduct a periodic inspection of the energy control procedure at least annually to ensure that the procedure and the requirements of this standard are being followed.
Right alongside training and communication lies the follow-up protocol of periodic inspections. You’ve outlined and defined your procedure, trained and retrained your employees, and equipped them with what they need to get the job done safely and efficiently. But it doesn’t end there. Not only do employees come and go, but so does your equipment and the skill sets of the employee if the task is not performed on a regular basis. Annual auditing is a key component of maintaining your LOTO program in highest regard for safety and productivity.
Periodic inspections/audits will help companies maintain the established procedures to minimize risk along with maintaining compliance, and ultimately protecting the investment of the safety program. The purpose of an annual audit is to verify all required procedure are in place, accurate, effective, and optimized to the ideal lockout process. Inspecting each employee on the proper lockout process and retraining employees is vital in order to achieve effective execution of the program. Companies should also provide comprehensive documentation of these annual audits being conducted and keep these records of dedication to protect their investment in the program, as audit records and documentation are compliance requirements as well.
The three steps to a successful audit program include meeting the appropriate frequency of annual periodic inspections at a minimum, ensuring authorized employees are competently trained to audit, and certifying that the inspections are being performed with proper documentation.
When it becomes boiled down to these three components, it begins to become apparent that a large factor of the
LOTO Standard 29 CFR 1910.147 “Control of Hazardous Energy” code violations are a direct result of human error and lack of company oversight.
Electrical safety goes beyond legislation and compliance. An environment that is highly productive and efficient is a culture where employees are secure, safe and cared for. According to the U.S. Department of Labor, a safe and healthy workplace not only protects workers from injury and illness, it can also lower injury/illness costs, reduce absenteeism and turnover, increase productivity and quality, and raise employee morale. In other words, safety is not just a good practice, it is good for business.
4) 300 Violations
1910.147(c)(1) Energy Control Program
The employer shall establish a program consisting of energy control procedures, employee training and periodic inspections to ensure that before any employee performs any servicing or maintenance on a machine or equipment where the unexpected energizing, startup or release of stored energy could occur and cause injury, the machine or equipment shall be isolated from the energy source and rendered inoperative.
The purpose of the Energy Control Program is to provide written policies and rules within your safety management system. This regulation addresses the practices and procedures necessary to disable machinery or equipment that will prevent the release of hazardous energy while employees perform servicing and maintenance activities. The way the procedure is documented can make a big difference to the person trying to carry it out correctly. The different types of procedure documentation is up to each company to determine which documentation format is going to be most effective for your employees and equipment.
When authorized employees are locking out equipment, it’s generally recommended to utilize a graphical format. Graphical procedures tend to provide the clearest, most easily accessible and visually appealing guidance. Proper location and identification of all energy sources is also essential.
By including high resolution photos of the equipment, isolation points, control points and specific shutdown components, authorized employees are able to quickly grasp how to lock out the equipment. Including graphical tags with this solution helps integrate the procedure with the isolation point and makes the lockout/tagout process much more efficient.
If your procedures include PESDs, you can document and provide training on the use and interpretation of these devices as part of the LOTO procedure for the specific equipment they are installed on. PESDs also are available to be installed with custom warning labels. This greatly assists employees when performing LOTO on equipment that features voltage indicators and/or portals by decreasing their risk of exposure to hazardous energy.
5) 185 Violations
1910.147(d) Application Control
The established procedures for the application of energy control (the Lockout or Tagout procedures) shall cover the following elements and actions and shall be done in the following sequence.
1. Preparation for shutdown: Before an authorized or affected employee turns off a machine or equipment, the authorized employee shall have knowledge of the type and magnitude of the energy, the hazards of the energy to be controlled, and the method or means to control the energy.
2. Machine or equipment shutdown: The machine or equipment must be turned off or shut down using the procedures established for it to avoid any additional or increased hazards to employees as a result of the machine or equipment stoppage.
3. Machine or equipment isolation: All energy-isolating devices that are needed to control the machine’s energy source must be located. These devices must then be used to isolate the machine or equipment from its energy source(s).
4. Lockout or tagout devices must be affixed to each energy-isolating device by authorized employees. Lockout devices where used, must be affixed in a manner that will hold the energy isolating devices in a “safe” or “off” position. Where tagout devices are used, it must be affixed in a manner that will clearly indicate that the operation or movement of energy isolating devices from the “safe” or “off” position is prohibited. If the tag cannot be affixed directly to the energy isolating device, the tag must be located as close as safely possible to the device, in a position that will be immediately obvious to anyone attempting to operate the device.
5. Stored energy: After the energy-isolating device has been locked out or tagged out, all potentially hazardous stored or residual energy must be relieved, disconnected, restrained, and otherwise rendered safe.
6. Verification of isolation: Before any work begins on machines or equipment that have been locked out or tagged out, an authorized employee must verify that the machine or equipment has been properly isolated and de-energized.
How Can GracePESDs Fit into Your LOTO Program?
Voltage is the common denominator in an electrical accident or an arc flash; no voltage means no accident/arc flash. At Grace, our mission has always been to ensure that every electrical worker returns home safely to their family and loved ones. We are always striving for ways to improve the workplace electrical safety standards by developing innovative products and solutions that minimize the risk of electrical exposure.
PESDs are a result of a constant zeal to find simple, innovative and practical ways of developing electrically safer work conditions that reduce accidents, improve productivity, enhance compliance as well as foster a safety culture.
GracePESDs engineer out the risk associated with routine maintenance tasks allowing it to be safely conducted from outside of the electrical cabinet, inherently reducing the risk of arc flash and shock hazards significantly. When properly incorporated into a facility’s electrical and mechanical LOTO safety procedures, PESDs enhance compliance with NFPA 70E and OSHA energy isolation principles.
GracePESDs like the voltage indicator greatly enhance compliance with OSHA and LOTO.
By adding PESDs to your mechanical or electrical LOTO procedures, the risk of an arc flash occurrence or shock hazard is greatly reduced due to the indicator’s bright LED lights visually identifying voltage presence.
Similarly, voltage portals like the Safe-Test Point provide a high-impedance protected method of validating voltage presence or absence using a multimeter. With the installation of the Safe-Test Point and Voltage Test Station, customers have reported their LOTO procedures have reduced from a 1 hour, 2-man operation down to a mere 5 minute, 1-man operation. This is a direct reflection of OSHA’s Office of Regulatory Analysis which states that
“For every $1 invested in safety and health programs, companies can expect a return of $4-$6 dollars.”
Based on a recent electrical safety survey conducted with PESD users, the results found PESDs reduced electrical LOTO tasks an average of 20 minutes and reduced mechanical LOTO tasks by an average of 23 minutes.