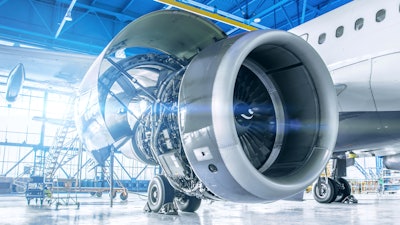
Quality control is crucial for any manufacturing process, but aerospace companies face higher standards than most. Faulty airplane components can lead to costly regulatory proceedings and even endanger lives. In light of this risk, aerospace quality control is imperative to get right.
Mistakes and flaws can arise at many points throughout the supply chain and production. While that may be an intimidating prospect, it also means many opportunities exist to refine aerospace manufacturing’s quality assurance (QA). Here are some of the best solutions.
AI-Aided Design
Aerospace quality control begins in the design phase. Artificial intelligence (AI) features in digital design software can suggest changes to early models or create preliminary designs for aircraft components. Because AI is better at detecting subtle trends in complex data, it can highlight faults humans may overlook.
AI in the design phase adds further value through virtual testing. Machine learning can simulate multiple scenarios in minimal time to test a digital design’s performance without expensive, real-world tests.
This combination of speed and in-depth analysis yields more reliable parts without extending production timelines. Some aerospace companies have noticed safety improvements of up to 30% and 75% shorter production timelines after implementing this technology.
Material Selection
After creating an ideal component design, aerospace manufacturers can ensure quality by choosing the right materials. Aluminum is a common choice, as it’s lightweight and corrosion-resistant, but some internal parts may benefit from softer, more flexible or hardier materials.
There’s no one answer to the best material for every component, and AI can once again help find the solution in each instance. Testing different materials in the same design in AI-assisted virtual simulations reveals how each will behave in the real world. AI can also compare these results to cost and availability analytics to highlight ideal options.
Right-sizing materials to specific components offers more QA than relying on industry standards or using the same resources for everything to reduce costs. AI’s speed in testing offers that reliability while lowering its development costs to justify it economically.
Supply Chain Transparency
After the supply chain, aviation companies must turn to their suppliers. Supply chain transparency is crucial to aerospace quality control, as counterfeit parts are surprisingly common. In 2023, all major U.S. carriers discovered they had fraudulent parts in their aircraft that entered the supply chain through falsified paperwork.
Partnering only with well-established, trusted suppliers is a good start, but even these companies can suffer from fraud. Counterfeiting aside, transportation or production errors can affect component quality before manufacturers receive the parts. Transparency-focused technology is the solution.
Internet of Things (IoT) tracking solutions can provide real-time location and shipment quality data to ensure safe transport. Blockchain platforms can offer immutable records of a part’s origin and shipment history to prevent fraud. These solutions are expensive, but their impact on QA is difficult to overlook.
Error-Resistant Workflows
A manufacturer’s internal workflows deserve attention, too. One of the most important steps in improving QA in these processes is to design them to contain less room for human error.
Automation minimizes human error risks, but it’s not the only solution. It’s also important to consider that robots may make mistakes more likely in some cases — namely when workflows are less consistent or predictable. The key is to design and assign production tasks to humans and robots according to their strengths and weaknesses.
Highly repetitive tasks with little to no variation are best to automate. Human workers can improve automation’s reliability by ensuring parts are aligned correctly and feature no defects earlier in the workflow. Designing production lines so each step can only proceed if everything is correct — like using physical stops to keep all parts in the same orientation — also helps, as it removes error-producing variability.
Standardization and Consistency
Similarly, aerospace manufacturers must ensure consistent conditions throughout their facilities. Standardization minimizes the risks of mistakes, but changing conditions can make even highly standardized processes less predictable.
Temperature fluctuations can affect some material’s performance under different stressors. Changing humidity can hinder robotic sensors’ reliability. Addressing these concerns and creating more consistent working conditions helps manufacturers ensure their other standardization efforts have the desired effect.
IoT devices are a helpful resource in this area of aerospace quality control. Smart HVAC systems can adapt to real-time data to ensure consistent temperatures and humidity as influencing factors shift. Equipment-monitoring systems can alert manufacturers of potential maintenance issues to address before they cause production errors.
Automated Quality Inspections
Quality inspections at the end of the production line are also important. However, conventional, manual approaches are too unreliable and inefficient to guarantee the level of assurance aircraft components need. Automated quality control is the better option.
Automated systems can perform visual inspections and more complex processes like Eddy current testing — one of the most common nondestructive testing methods in aerospace — faster and more accurately than humans. This accuracy stems largely from the fact that machines can’t get distracted and refer to the same data every time.
In addition to being faster and more accurate, automated quality testing creates data on each inspection. Over time, defect data will reveal larger trends, helping identify where problems come from for more effective process improvements.
Ongoing Testing and Optimization
Aerospace quality control isn’t over once parts leave the production line. Manufacturers must continue testing their products and internal processes to find areas to improve. It’s virtually impossible to eliminate defects entirely after one change, so ongoing optimization is necessary to slowly reduce these risks.
AI is once again an ideal tool for this task. Machine learning models can analyze digital twins of production workflows to identify bottlenecks or error-prone processes and suggest potential improvements. Similarly, predictive maintenance engines can improve quality over time by enabling optimized equipment repair schedules.
Some manufacturers have achieved a 100% quality rate despite using 30% fewer tests by optimizing their workflows through AI-driven insights. Applying similar tools to aircraft production would dramatically improve long-term QA results.
Aerospace Quality Control Is a Complex Undertaking
Aerospace quality control faces more obstacles and higher standards than QA in many other sectors. Manufacturers must capitalize on new technologies to navigate these challenges.
Achieving the highest possible quality standards requires attention to the entire supply chain and production process. Tackling issues at each phase will ensure a much higher level of consistency and quality.