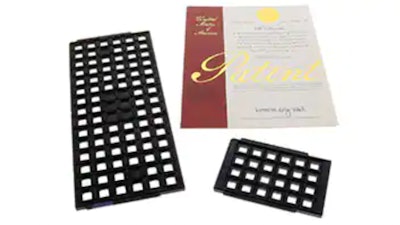
Digi-Key is one of the largest suppliers of electronic components, but that doesn’t necessarily mean its customers always place massive orders. The company allows customers to order fewer than the minimum manufacturer quantities of components.
Even with smaller orders, though, Digi-Key needs to ensure components are packaged safely. And that sometimes means using full-size JEDEC trays, big bags and big boxes to send single pieces, which Digi-Key engineer Shane Heinle called “a costly overkill predicament.”
So Heinle and fellow Digi-Key engineer Reid Landsrud set about finding a solution for giving customers their products in the “original” packaging while cutting back on shipping materials. The two came up with a JEDEC tray, which is a flat storage system (typically made from molding compounds) that adheres to standards for handling and transporting integrated circuits, that’s one quarter of the regular size.
“We elected to design the tray to hold the quantities of product we needed most and based the different pocket sizes on the JEDEC standards for the [integrated circuits], making it as versatile as possible,” Landsrud said.
Because of their work, Digi-Key was awarded a U.S. patent for a safer and more efficient way of transporting integrated circuits.
We recently caught up with Heinle and Landsrud to discuss the years of development that went into perfecting the smaller tray along with potential benefits to clients and the environment.
IEN: Making the trays smaller seems like such a simple concept. But can you explain everything that went into actually implementing these smaller trays?
Heinle: The complete work took Reid and I about five years. There were many questions that we started asking like, “What is this packaging going to look like?” “What is the best way to do this?” “What material do we use?” and “How are we going to make it?”
I had visited with one of our suppliers, Conductive Container Inc (CCI) in New Hope, Minnesota, and they talked with their packaging engineers and 3D printed a piece of material with a pedestal that would grasp the body of the component. I thought that was amazing. I knew Reid worked internally with our 3D printers so I asked Reid if he could print me a couple designs that I had drawings of, to see what the physical size would be. That was when Reid asked the question “Why don’t we use the same cavities as the current trays?” and my mind was blown. I thought why am I trying to reinvent the wheel when there are already standards on component sizes. My next question was, “Reid, can you help me?”
The first thing we did was start asking people we knew in the industry if there were any thoughts already out there. We also started conversing with many different engineers at Digi-Key. We pitched our idea to them, and they all offered their ideas, experience and knowledge which really helped us move forward with the idea. Reid had some knowledge of injection molding and taught me a lot about it, so we started asking that type of question to our contacts in the industry.
The turning point was when we had a conversation with CCI. They had found a tool manufacturer in Wadena, Minnesota, by the name of Holland Molds Inc. Reid and I, from Thief River Falls, Minnesota, and our CCI colleagues, from New Hope, all drove to Wadena and met with Holland Molds. We presented our idea to them and they immediately stated it would be possible for them to make a tool for us.
Now that we had some more information on that, we had some homework to do. Reid started researching the trays, sizes, etc., and I started on quoting tooling companies. We had regular meetings to discuss the drawings and how components would sit in the trays – one hour each Friday for about one year.
We also had regular conversations on who would help us. I talked with many different tooling manufacturers and injection molding plants. I received numerous questions from tool makers in Asia and stateside. Reid and I presented this to our leadership team at Digi-Key and they were instantly intrigued by it and started asking very good questions.
After many months of research and discussion we found our path toward the start of this concept. We found material from RTP in Winona, Minnesota, that we qualified for use with our components, and we decided that CCI and Holland Molds were the best companies to partner with on this project. We made it a completely Minnesota-based project and kept everything local.
Landsrud: Shane and I put a large amount of effort into these trays. We started with the general idea, design and prototyping. We 3D printed several prototypes to verify our designs. We put a lot of effort into tolerancing and dimensional verification of our designs to make sure that we would not damage any product when shipping parts in these trays.
We worked with CCI, the injection molder, to help identify a molding process and a mold maker that would work with us to move this to manufacturing. They introduced us to Holland Molds, the company that machined and designed the injection molds. Both of these companies helped us with the design for manufacturing aspects of the trays. We spent a substantial amount of effort making sure that the design of the mold and the injection process would produce the tray that we wanted.
All of the above happened while we were working internally at Digi-Key to get the trays approved.
IEN: Can you explain how the trays are reducing the impact on the environment and any other benefits they provide?
Heinle: These trays are protecting the product from damage. The safest way to package the product is in the exact packaging used by the manufacturer, but how do we make sure our customers receive product that isn’t damaged? If damage occurs, then Digi-Key is sending replacements. Any time you send replacements, now you are causing more emissions for transit a second time. If rework is needed, now you are causing additional resources to be used for the rework of boards. More time and money have to be spent by all companies due to damage which could have been prevented immediately.
Less packaging materials are being used. Smaller bags and smaller boxes are being used with these quarter trays as compared to using a larger bag and box for the full-sized trays. This also leads to less space used during transit and less material our customers need to dispose of or recycle.
Landsrud: If we look at this from a materials used standpoint, these trays are much smaller than the JEDEC standard trays that are generally available, using much less plastic. Our smaller trays, when packaged properly, fit in a much smaller moisture barrier bag (think 5” x 8” versus 10” x 20”), which means another reduction in plastic usage. Since they are packed in a smaller moisture barrier bag, they require less desiccant to be packed with the parts to keep them dry.
If we were to consider a single detail order containing parts that would ship on this tray, a much smaller box can be used for shipping (9” x 9” x 2” vs 21” x 7”x 4”). Less packing material is required to safely transport the product. Using less materials in total also means there is less for our customers to dispose of once the product is received.
From an inbound to Digi-Key point of view, we order less of the JEDEC standard trays as they are replaced by our trays. The standard JEDEC trays are typically manufactured close to where the ICs are manufactured, in southeast Asia. The fewer JEDEC standard trays we use, the less we consume in shipping resources.
Our trays are manufactured in New Hope, Minnesota, and consumed in Thief River Falls, Minnesota, a short shipping venture.
In addition, the trays we designed hold the opportunity to lend themselves well to automated machinery that will place the parts on circuit boards, especially the type of machinery that would produce small batch runs. The trays are also compact, making long-term storage of small quantities of these ICs less space consuming.