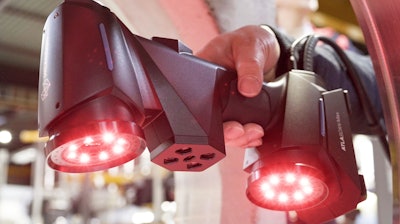
According to IMTS β the International Manufacturing Technology Show β this Septemberβs conference and expo is βwhere the creators, the builders, the sellers and the drivers of manufacturing technology come to connect, be inspired and find solutions.β
Some such solutions address long-standing needs for industrial designers. One of these is the latest from Hexagonβs Manufacturing Intelligence division: a new handheld 3D scanning technology that enables engineers and manufacturing personnel to easily scan what they need in a wide range of environments inside and outside factory walls.
Two new handheld devices, the ATLASCAN Max and MARVELSCAN, are highly portable, making them ideal for applications where metrology has not typically been used. IEN spoke with Joel Martin, Hexagonβs director of metrology devices for North America, to learn more about what the technology will bring to the market.
IEN: Tell us a little bit about this latest tool and what you're most excited about as it pertains to the new features and benefits.
Joel Martin: Historically, scanners have been very one-size-fits-all. So everybody looks for sacrifices in certain areas of their workflow. That could be portability, that could be accuracy, that could be resolution, that could be speed, that could be ease of use, all of these individual things. And now, through the release of the two new handheld scanners, I feel we really have the opportunity to not need to deal with these sacrifices. You can start to pick truly what is the right tool for what you're trying to do and optimize all of those opportunity areas around what's most important as a manufacturer, as a designer and implement the right technology the first time through, rather than just try to solve your problem with whatever technology is available to you at that point in time.
IEN: So you can have it all?
JM: Absolutely. The handheld sensors are really all around speed, portability and ease of use. Youβre not trying to use some overly complicated device for a task that may not require that level of advancement.
Joel Martin, HexagonHexagon
Agility is the second one, and agility is really around being able to take the scanner to the part and being able to understand βwhat am I measuring and where am I measuring it?β So you're not necessarily bringing a part to ameasurement device, you're going out and you're measuring the part on the shop floor in the manufacturing process. And that could be in extremes. So in casting an assembly and stamping in these hugely rough environments where metrology didn't really live before, we've created a group of sensors that are far more impervious to the environment that they measure in.
And then, of course, the last one being simplicity. This is really around ease of use and entry level operators lowering the barrier of entry to high technology scanning and to getting metrology grade data into a process further upstream and more usable than it was before.
IEN: The piece about ease of implementation, lowering the barrier of entry in terms of skills, that was a really interesting component of this for me. Obviously, the industry is dealing with a ton of workforce gaps. Were your customers asking you for this?
JM: I think it's twofold. It's both the aging workforce that is retiring and taking a lot of legacy knowledge with them and the younger workforce coming in that is expecting technology to work for them rather than expecting to have to work around the limitations of technology. And I think that's a bit of a paradigm shift in generations. You had some of the legacy knowledge: quite frankly, some of these guys are quite proud of how they've managed to create solutions where there are no technologies to solve this. And you look at some of the younger generation coming in who have a different level of expectation of what technology can do and look at it and say, βno, I shouldn't have to work around this. The technology should work for me here.β
So that's something that not just our customers have seen and requested, but even, as an OEM, we've seen as well. These are all things that are part of our product development process of making sure that we're not just building cool devices, we're building things that are solving industry problems.
IEN: I totally agree, and I think that tech tools seem to be now the best way to target worker retention. It eliminates frustration in people's jobs. It makes them feel like they're contributing something cool and adding to their skill set and using technology and that's what the younger generation wants.
JM: Yeah, absolutely. And it is something that we've targeted a lot in these two scanners specifically. The way that the human operates with the technology is more like a video game than it is like a CNC machine. So we've really tried to take the technology and make it work in a way that is so simple and easy to understand that you don't need a PhD behind you running you through the process of what's going on. You're sort of just figuring it out as you go because the ease of use is there to determine your way as you figure it out.
IEN: I'd love to talk further too about the way the device fits into some of the larger shifts in technology that is happening with industrial companies. What are the priorities of the customers that you're targeting here and how did all of that factor into how you develop this tool?
JM: I think one of the big priorities is around just collecting more data, being more aware of what's going on in your manufacturing processes and being able to track that and adapt to that. And you see this throughout the industry. With IoT and the whole process of trying to collect more data more frequently throughout any process, scanning has always been one of those bottlenecks because it has been a more challenging process to do. It requires high tech equipment and skilled operators and sometimes even specific environments. So, in order to keep up with how quickly our customers want to move, all of that drives us in the technology that we're building and making sure that it fits those requirements.
Visit Hexagon at IMTS booth #134102 or learn more at https://hexagon.com/company/divisions/manufacturing-intelligence.